In the vast world of textiles, the term 'neps' might sound perplexing to those outside the industry. Yet, for manufacturers, these tiny knots are a significant concern. Neps are small clumps or rivulets of fibers tangled together, which can occur during various stages of processing. They can impact the appearance, consistency, and quality of yarn and fabric.
Understanding why neps occur and how they can be managed is vital for producing top-notch textiles that stand the test of time and quality benchmarks. In the textile-rich landscape of India, where craftsmanship meets innovation, addressing neps can enhance product quality and reputation. This article explores what neps truly are, practical reasons for their occurrence, their effects on textile quality, and strategies to minimize their presence for superior fabric production.
What Are Neps?
In the intricate dance of textile production, a seemingly small nuisance known as neps can have a ripple effect on the final product. But what exactly are these neps? Simply put, neps are tiny clusters or knots that occur when fibers become entangled during various stages of textile processing. This tangling creates lumps that are often hard to remove completely, and they can emerge in both natural and synthetic fibers. Though they might appear innocuous, these clusters can dramatically alter the look and feel of fabrics, leading to inconsistencies and unwanted textures.
The origin of a nep typically traces back to the raw materials or the early stages of fiber processing. For example, in cotton, a common source of neps is the condition of the cotton boll and the process it undergoes from picking to cleaning. The presence of immature or short fibers can easily entangle and become neps during mechanical processing. Such variations require careful handling and attention during manufacturing to ensure a smoother, more uniform product.
A surprising aspect of neps is how they reveal deeper stories about fiber quality and handling. Aspects like fiber length, maturity, and even moisture levels can influence nep formation. For instance, high moisture content during processing might cause fibers to clump and twist together more readily. Mechanical stressors like carding or spinning can exacerbate these issues, making it crucial for manufacturers to monitor each stage closely to minimize their occurrence.
Why Neps Matter
The presence of neps is more than a mere aesthetic issue; they can affect the functionality and performance of the fabric. In making yarns, consistency is key, and any nep can lead to weak spots or inconsistencies that can compromise tensile strength. Moreover, the final fabric could feel rough or uneven to the touch. This is why understanding and combating neps is an integral process in textile quality assurance. Neps not only mar the appearance but also affect dye uptake, potentially causing spotty or uneven coloring during the dyeing processes.
"In the world of textile innovation, understanding the micro-structures like neps can set a foundation for better quality and durability," says textile expert Dr. Priya Varma.
Given their subtle yet pervasive impact, identifying and managing neps requires continuous research and technological advancement. Across India, textile manufacturers are increasingly employing new techniques and tools to detect and mitigate the impact of neps. As the industry grows and evolves, understanding these tiny knots can make a huge difference in maintaining India’s reputation as a leader in high-quality textile production. Mastering the management of neps ensures not only superior quality but also enhances customer satisfaction, making them a key focus area for any textile business aiming to excel.
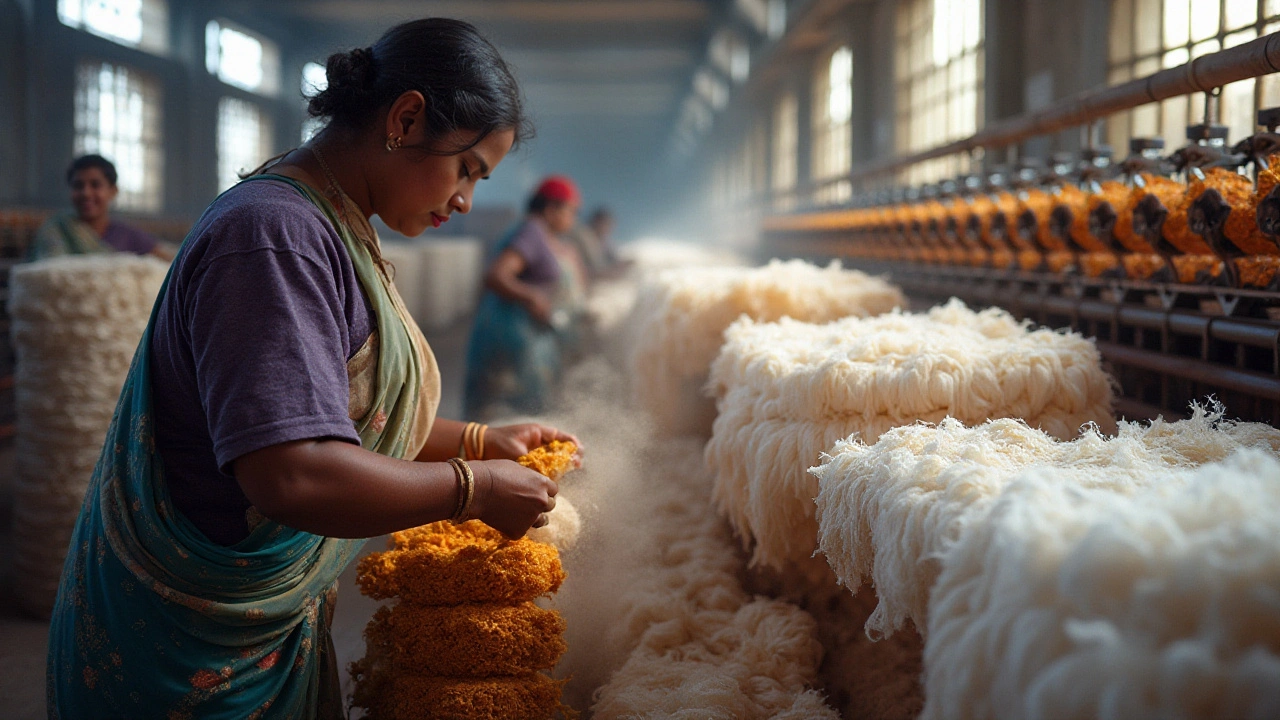
Causes of Nep Formation
Understanding why neps occur in textile manufacturing processes is crucial for anyone involved in this industry, especially in a competitive market like India’s. Neps, these tiny but troublesome clumps, can severely compromise the aesthetic and functional quality of textiles. Several factors contribute to the formation of neps, starting from the beginning of the fiber lifecycle. Raw materials play a significant role; fibers that are naturally curly or have a high degree of crimp, such as cotton, are more prone to neps. Inconsistencies in fiber quality, such as varying lengths and diameters, can exacerbate the situation, leading to increased instances of nep formation.
Handling of the fibers during harvesting and storage is another critical phase. Improper harvesting techniques can damage the fibers, causing them to knot together. Similarly, storing fibers in humid or overly dry conditions can affect fiber elasticity and strength, leading to brittleness and increased likelihood of neps. Mechanical processing, especially during the carding phase, is notorious for promoting nep formation. When fibers are carded too aggressively, the mechanical forces can lead to tangling, creating these unwanted knots and lumps. The machinery's maintenance and settings also hold significant sway; poorly calibrated or ill-maintained machines tend to produce more neps.
An expert in textile engineering, once stated,
"The presence of neps is often an indicator of the need for process optimization. Addressing mechanical and material factors is key to reducing defects."The human factor and operational efficiencies should not be overlooked either. Operator expertise in managing machinery settings to adapt to different fiber types can directly influence the presence or absence of neps. Training operators to be vigilant about correct settings, and maintaining an environment that is conducive to fiber stability, can reduce nep creation. Some manufacturers also employ advanced technologies such as nep detectors, which help in identifying high-nep-producing areas in real-time. Adopting a holistic approach that considers raw material quality, processing accuracy, and operational excellence might be the key to minimizing neps.
Exploring new technologies and materials is also a forward-looking solution. Currently, industrial researchers are experimenting with genetically modified cotton that has longer, stronger fibers, lessening the probability of nep formation during processing. Utilizing advanced spinning and carding machinery designed to gently handle fibers without introducing stress is another area gaining traction. A table below elaborates some findings from recent studies about the impact of machine settings on nep formation:
Process Stage | Impact Factor | Effect on Neps |
---|---|---|
Carding | High Speed | Increase |
Spinning | Temperature Control | Decrease |
Harvesting | Hand vs. Mechanical | Varies |
In the realm of textile manufacturing, especially in places like India where precision and tradition coalesce, understanding the science behind nep formation can drive improvements. By focusing on raw materials, technology, and human expertise, manufacturers can aspire to produce textiles with superior quality and consistency.
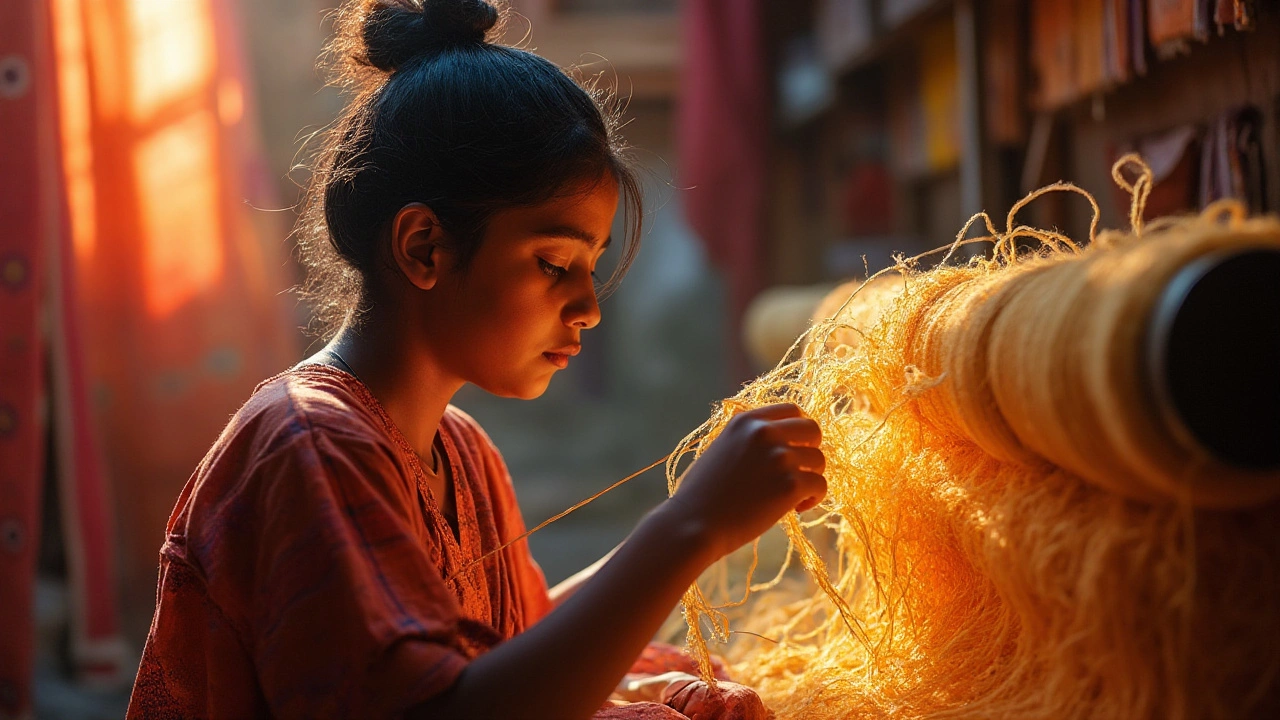
Impact of Neps on Textile Quality
Neps in textiles, those seemingly innocuous lumps of fiber, can have a considerable impact on the quality of yarns and fabric. When present in yarns, they interrupt the smooth texture, leading to an uneven and rough surface in the final woven or knitted fabric. This disruption not only diminishes aesthetic appeal but also affects the tactile quality, leading customers to perceive such fabrics as being of low quality. In an industry where touch and appearance often dictate buyer sentiment, neps can make a crucial difference. It’s like finding small knots in a supposed-to-be smooth silk scarf; it simply doesn't meet the premium expectation.
Moreover, neps can affect dyeing processes, leading to dye spots or uneven coloration in fabrics. This happens because the tight entanglement of fibers within neps may not absorb dyes as effectively as the surrounding fibers, causing coloration irregularities that are often undesirable. Patchy dyeing becomes particularly problematic in vibrant colors, where consistency in shade is paramount. Neps thus necessitate re-dyeing efforts or even the discarding of affected batches, escalating costs unnecessarily. David Knott, a leading textile engineer, once remarked,
"The presence of neps can easily betray the most tasteful of designs, leaving manufacturers with the choice of either investing in improved quality control or risking their market reputation."
Another aspect often overlooked is how neps alter the mechanical properties of fabric. Fabrics with numerous neps tend to have reduced tensile strength and elasticity, as the smooth integration of fibers is hindered. This problem is compounded when these fabrics are subjected to mechanical stresses during garment manufacturing or through everyday use, making them more prone to tearing or deformation. In technical textiles, where material properties must meet rigorous standards, neps could even result in compliance failures, risking not only product rejection but also potential safety concerns.
It’s crucial for manufacturers to address these impediments to maintain and optimize the performance and appearance of their products. Customers today are more discerning, seeking not only value but also a story of precision and quality in the fabrics they choose. Hence, the continuous challenge for manufacturers lies in identifying early signs of neps during the production process, employing advanced sorting and processing techniques, and ensuring each spool of yarn is not compromised. By addressing neps effectively, textile manufacturers in India can not only enhance product appeal but can also tap into premium markets demanding top-tier textile performance.
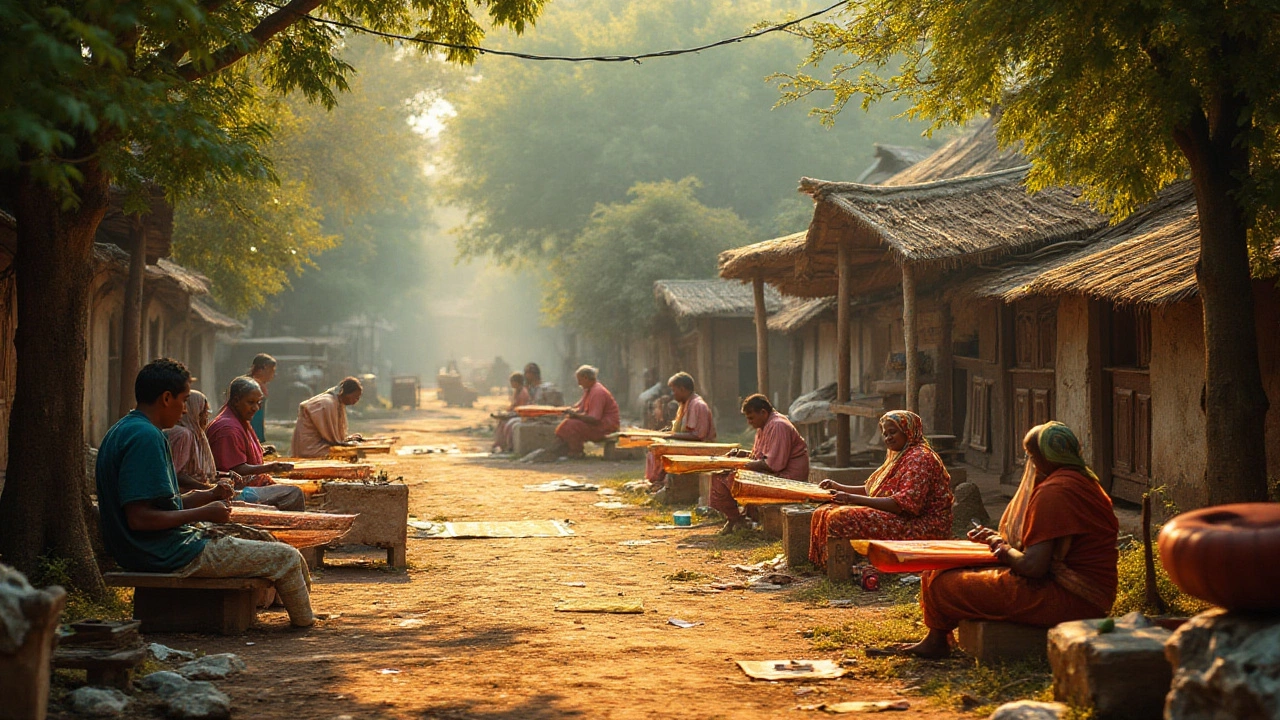
Techniques to Manage Neps
When it comes to crafting high-quality textiles, controlling neps is paramount. Fabric manufacturing is a meticulous art, where every detail counts, and neps, those small entangled fiber knots, can be a nuisance lowering quality and value. To manage these effectively, manufacturers must employ an array of techniques across different stages of production. First, utilizing high-quality raw materials forms the baseline. The choice of fibers directly impacts the texture and uniformity of the yarn. Selecting fibers that are both long and fine can drastically reduce the chances of nep formation. During the ginning process, gentle handling is critical. Rigorous mechanical treatment can exacerbate nep formation by twisting and knotting fibers unnecessarily. Hence, moderating speed and pressure can mitigate this risk.
One effective method is optimizing the carding process—often characterized as the heart of spinning. Carding helps in detangling fibers, aiding in smoother and less knotted strands. Advanced machinery equipped with precise settings can greatly influence outcomes here, promoting consistent and high-quality cards with fewer neps. Regular maintenance and calibration of machines ensure they operate efficiently, reducing the chance of mechanical faults that could intensify nep creation. Another vital factor is humidity control, which often goes overlooked. Maintaining optimal humidity levels in production environments can influence fiber behavior significantly. It ensures fibers remain supple and less prone to drawbacks like static electricity, which can cause fibers to bunch up.
Incorporating quality control measures at each phase of the process also bolsters efforts against neps. Employing a systematic approach wherein each batch of yarn is scrutinized can help in quickly identifying inconsistencies and allowing for corrective actions. Implementing real-time monitoring systems adds an extra layer of assurance, providing immediate feedback on the fiber conditions as they're processed.
"Quality control isn't about stopping problems after they occur; it's about preventing them from happening," says textile technology expert Dr. Laura Greaves.One can't overlook the importance of skilled labor. Training employees to recognize different fibers and how they react in the production stage empowers them to make adjustments promptly, ensuring lesser wastage and defects.
Finally, testing completed yarns and fabrics for neps is vital to maintaining high standards. Various testing methods are available, from visual inspections, where skilled workers examine fabrics under ample light, to computerized testing instruments that provide quantitative data about nep concentration. This information is invaluable, offering manufacturers insights that guide future production cycles, refining processes for better outputs. By integrating these techniques, textile manufacturers can significantly reduce the incidence of neps, thereby enhancing yarn and fabric quality and establishing their mark as industry leaders. Employing well-rounded strategies ensures that each piece of fabric produced is nothing less than a masterpiece of artistry and engineering. Addressing neps at every step not only uplifts the quality but also strengthens the reputation of the textile manufacturing sector in India.