So, ever wondered why some factories run like clockwork while others seem to hit a snag every other hour? A lot of it boils down to how well they manage and organize their production processes. Enter BOM and MOM, two concepts that might sound jargon-y but are actually super essential in keeping things humming smoothly on the manufacturing front.
First up, the BOM or Bill of Materials is exactly what it sounds like—a detailed list of all the parts and materials you need to make your product. Picture it like a recipe for a cake; you need exact ingredients in precise amounts to bake it just right. In manufacturing, that ensures nothing is missing and prevents last-minute hitches.
- Basics of BOM and MOM
- Importance of BOM in Manufacturing
- Role of MOM in Production
- Real-life Applications of BOM and MOM
- Tips for Optimizing BOM and MOM
Basics of BOM and MOM
Alright, let’s break it down. Think of a factory as a giant, complex system. To get everything working smoothly, two key players come into play: the BOM and the MOM. These acronyms might sound a bit robotic, but without them, factories would be chaos zones.
The BOM, or Bill of Materials, is basically the master list for creating your product. Imagine building a car. The BOM will include everything from the tiny screws to the big components like the engine. It details not only what parts are needed but also how many and what specifications they should have. It's like having your shopping list ready before hitting the grocery store.
On the flip side, we have MOM, which stands for Manufacturing Operations Management. MOM is all about managing the daily operations needed to produce those BOM-listed items. It covers scheduling, production processes, quality checks, and everything else that keeps the assembly line moving efficiently. Yes, a bit like being both the coach and the manager in a football game ensuring every play is executed just right.
Can’t see how they’re interlinked? Let’s visualize this: say you’re assembling a bike. The BOM would list the frame, wheels, seat, etc., and the MOM dictates the order they’re assembled, how fast it should happen, and checks for any issues like wheel alignment.
In simple terms, while the BOM lays out ‘what’ is needed, the MOM focuses on ‘how’ it’s all put together efficiently. Both are crucial for ensuring a well-oiled production line that meets quality and quantity goals. Keeping these two aligned and updated is like having a roadmap and guide rolled into one, crucial for manufacturing success.
Importance of BOM in Manufacturing
When you're knee-deep in the production world, the BOM (Bill of Materials) is like your best buddy—it helps you keep track of every little thing you need to get a product from start to finish. It's not just a shopping list; it's a roadmap for manufacturing success.
Think of a well-put-together BOM as your secret weapon against chaos. It lays out every component—down to the screws and nuts—so nobody's left scrambling last minute. When every widget and gizmo is listed, purchasing becomes way more efficient, saving both time and money. This detail-oriented approach helps you stick to a budget and meet deadlines like a boss.
BOM isn't just for ordering parts. It's a treasure trove of knowledge for everyone in the supply chain. Engineers can reference it to avoid confusing one part for another, and quality control experts use it to ensure everything meets standards. Plus, it's the backbone for calculating raw material costs; so, you can easily adjust pricing strategies if costs fluctuate.
And if you're making changes or rolling out upgrades? The BOM makes the transition seamless. You update a single document, and everyone knows what to do. In a world where time is money, this kind of efficiency can be a game changer.
Component | Estimated Cost |
---|---|
Resistor | $0.10 |
Capacitor | $0.20 |
Totally worth the effort, right? Getting your BOM sorted upfront is one of those 'work smarter, not harder' moves that's invaluable in manufacturing.
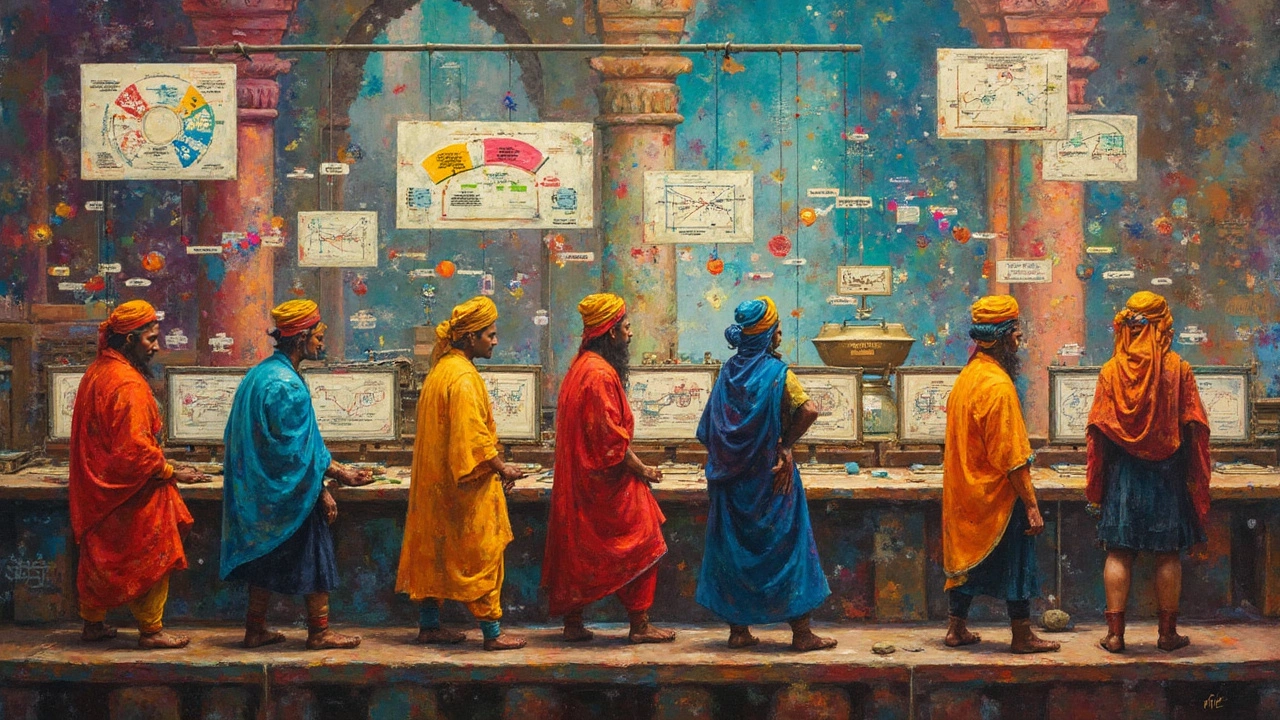
Role of MOM in Production
When it comes to manufacturing, Manufacturing Operations Management (MOM) is like the secret sauce that keeps the production line optimized and running smoothly. Imagine MOM as the grand master planner ensuring everything on the factory floor works like a well-oiled machine. It isn't just about moving things around; it's about strategically improving every part of the process.
MOM's job covers a broad range of responsibilities. It includes managing production schedules, maintaining quality control, and overseeing inventory management. Basically, it synchronizes all the moving parts so the production line can churn out products without unnecessary delays or hiccups.
According to a report from the Manufacturing Leadership Council, companies that adopt MOM solutions see an average increase in productivity by up to 20%. That's a significant boost, right? One of their experts notes,
"Implementing effective MOM strategies can be the difference between just surviving and truly thriving in the manufacturing sector."
What sets MOM apart is its emphasis on data-driven decisions. By using real-time data, MOM helps manufacturers pinpoint inefficiencies and tackle them before they become big problems. This proactive approach means fewer downtimes and higher production rates.
- MOM ensures compliance with regulatory requirements, which is crucial in industries like pharmaceuticals or automotive.
- It integrates seamlessly with existing ERP and MES systems, making it easier for companies to harness its full potential without overhauling their entire infrastructure.
In essence, investing in a robust MOM system might just be the best thing a manufacturing company can do for its bottom line. Whether it's improving quality, reducing waste, or just making sure everything gets to the right place at the right time, MOM's got it covered.
Real-life Applications of BOM and MOM
You might think that BOM and MOM are just concepts hanging around textbooks, but they're actually the backbone of manufacturing magic happening daily worldwide. Let's break down how they make a significant impact on the production lines.
Let's start with BOM. Think about your daily gadgets like smartphones or laptops. Each of these gizmos is a result of a meticulous BOM. The smartphone BOM will list every single component, from the microchips to the screws. Manufacturers use this list to make sure they have everything needed before assembly starts. It prevents delays because nothing kills productivity faster than missing parts!
Now, shift gears to MOM, which is about how you get things done efficiently and correctly. Imagine a car factory that's assembling vehicles around the clock. MOM technology helps streamline production by managing tasks like scheduling, equipment maintenance, and quality control. It's like the conductor in an orchestra, ensuring each part of the manufacturing process is in harmony. If you’ve seen automated robots working in car plants, MOM is the brain behind coordinating those moves.
In the field of pharmaceuticals, using both BOM and MOM is critical. Companies must track each batch's ingredients and document every production step meticulously for compliance with health regulations. Errors here aren't just costly; they can impact consumers' health.
Want a bit of number-crunching? Here's a quick peek at a typical BOM setup in electronics:
Component | Quantity | Supplier |
---|---|---|
Resistors | 150 | ABC Electronics |
Microchips | 10 | ChipTech |
Capacitors | 30 | ElectroParts Ltd. |
This table showcases how a straightforward BOM helps companies keep track of what's needed and from whom.
So, it's clear these aren't just terms for insiders. They dramatically refine how stuff gets made, reducing errors and fine-tuning processes. If you're in the manufacturing biz or just curious about how your favorite products come to life, understanding BOM and MOM is like having the cheat code for making products efficiently!
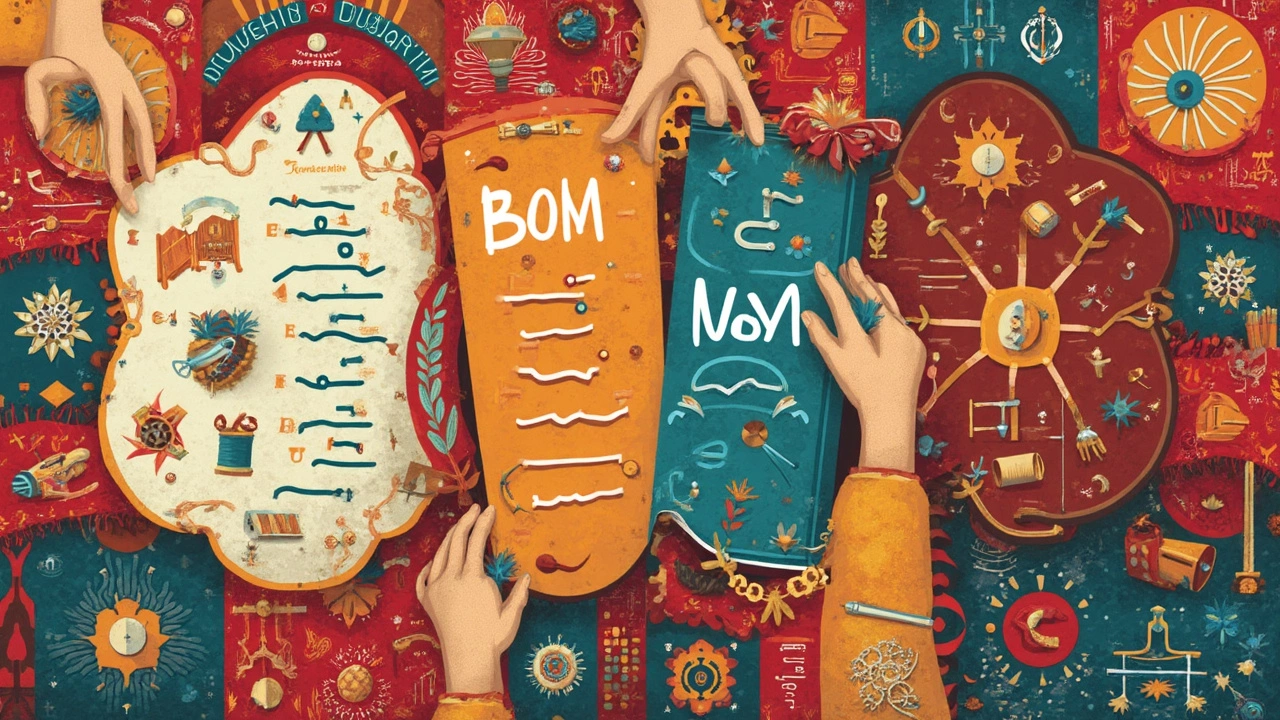
Tips for Optimizing BOM and MOM
So, you want to get the best out of your manufacturing process? Optimizing your BOM and MOM is a great place to start. Here are a few handy tips to ensure you're getting it right.
First, keep your BOM up-to-date. This might sound basic, but you'd be amazed at how quickly things can go off track if you're using outdated materials or parts lists. Make sure you regularly audit and update your BOM to catch any changes or improvements in components.
Next, consider automated software for BOM management. Software solutions are a lifesaver, reducing human error and speeding up updates. They ensure accurate tracking from the initial design right through to production.
When it comes to MOM, having clear communication lines is key. Make sure everyone from the design team to production workers knows the plan and their role in it. This helps you avoid misunderstandings and keeps production on schedule.
Also, take the time to map out your workflows clearly. By documenting each step, you can identify where things might bottleneck or slow down and address these issues proactively.
Step | Description |
---|---|
1. Regular Updates | Audit BOM frequently for any component changes. |
2. Use of Automation | Implement software to minimize errors in BOM management. |
3. Clear Communication | Ensure every team member understands their role in MOM. |
4. Workflow Documentation | Document steps to identify and fix bottlenecks. |
Finally, don't underestimate the power of feedback. Regularly check in with your team to identify what's working and what isn't. A few tweaks here and there based on ground-level feedback can significantly boost efficiency.