When it comes to building skyscrapers or crafting automotive frames, the quality of steel used cannot be understated. Each shining surface you see around is the result of an intricate dance of chemistry and innovation. The world of steel manufacturing is dominated by a handful of companies who continuously push the boundaries to set new standards in quality and robustness.
Exploring these manufacturers sheds light not just on their processes but also on environmental commitments and technological advancements that propel them ahead. As global demands evolve, so do the steel titans, with each step altering the landscape of this critical industry.
- The Anatomy of High-Quality Steel
- Key Global Players in Steel Production
- Innovative Techniques and Technologies
- Environmental and Sustainability Efforts
- Choosing the Right Steel for Your Needs
The Anatomy of High-Quality Steel
High-quality steel acts as the backbone of modern infrastructure and technology due to its strength, versatility, and durability. But what sets apart high-quality steel from ordinary variants? At the heart of these differences lie intricate processes of alloy composition, heat treatment, and stress testing, all of which work harmoniously to create an exceptional product. The blending of carbon with other elements like nickel, chromium, and vanadium at precise temperatures is a pouring of art and science. For instance, nickel lends resistance to corrosion, while vanadium improves strength, crucial for construction and automotive industries. Exploring the properties of high-quality steel unravels a story of both tradition and innovation. As Robert Nozick once said,
"Complexity answers complexity; it's a response as much as it is a design."
Attention to detail, from the origins of raw material to the meticulous manufacturing phases, is paramount. It begins with choosing the right raw iron ore, ensuring impurities are minimized and the ore sticks to rigorous standards. Once smelted, this ore transforms into pig iron, setting the stage for further refinement. It is during this phase where the smelting of iron with specific carbon ratios, and the incorporation of alloys unfolds. Careful blending alters the crystalline structure of the steel, enhancing its features like ductility and tensile strength, making it ideal for various applications. Environmental conditions during manufacturing, such as ambient humidity and temperature, can significantly affect the chemical reactions in steel production. In controlled settings, manufacturers ensure consistent atmospheres that lead to uniformly high-quality output, a factor that is often overlooked in commercial discourse.
Heat treatment follows, one of the most critical steps on the journey to high-quality steel production. By manipulating temperature exposure and cooling rates, manufacturers control the grain structure within the steel. Rapid cooling can increase hardness and strength, known as quenching, while controlled cooling, or annealing, enhances ductility. These treatments dictate mechanical properties and determine the steel's suitability for specific tasks. Aerospace components, for instance, require a precise balance of these characteristics to withstand extreme conditions while maintaining lightweight profiles. Temperature control throughout these processes is not just vital but crucial to preventing defects such as brittleness that could compromise safety and integrity. This attention to detail is a testament to the skill and care applied in steel crafting.
Lastly, stress testing remains a definitive phase in determining steel quality. This involves subjecting the steel to various conditions mimicking real-world challenges, such as tensile, compression, and shear tests. Such rigorous assessments ensure the material can endure anticipated stresses during its lifecycle, offering durability and reliability expected from high-quality steel. Facilities often utilize advanced technologies like ultrasonic testing and magnetic particle inspection, allowing manufacturers to detect minute cracks or inconsistencies not visible to the human eye. Steel quality becomes not just a label, but a quantifiable attribute, a reassurance of performance and longevity. Companies offering these exacting standards have won the trust of industries worldwide.
Key Global Players in Steel Production
Steel is the backbone of modern industrial development, and its top manufacturers wield significant power in shaping both the economy and infrastructure worldwide. Names like ArcelorMittal, Nippon Steel, and POSCO resonate deeply within the sector, each carrying a history of innovation and resilience. ArcelorMittal, headquartered in Luxembourg, is the world's leading integrated steel and mining company. Their prowess stems from a relentless pursuit to enhance steel quality, aided by advanced technologies that reduce costs and improve efficiency. In fact, their leadership in the industry has allowed them to produce a whopping 70 million tons of steel annually, setting a benchmark for others.
Nippon Steel, hailing from Japan, is another heavyweight in this league. Known for their innovation in high-quality steel production, they continuously develop new grades of steel that drive both industrial and technological advancements. The company's dedication is evident in how they tackle challenges such as environmental regulations and fluctuating market demands, always staying a step ahead. As they expand their global footprint, their investments in researcher and developer (R&D) and sustainability become central to their strategy. According to their CEO, "Innovation is not just about creating better products; it's about creating a better world."
Korea's POSCO stands out not just for its massive production capacity but also for its commitment to eco-friendly processes. Their ‘Green Steel’ initiative exemplifies the modern approach to steel manufacturing, where sustainability goes hand-in-hand with production. This can be seen in their reduction of carbon emissions by over 20%, a remarkable achievement in an industry often criticized for environmental impact. With ambitions to expand their influence in emerging markets, they continue to balance quality and responsibility.
These companies, while distinct in their strategies and markets, share common goals: improving steel durability, meeting demanding customer needs, and creating products that revolutionize industries. Their leadership is not just about production numbers but about steering the future of steel manufacturing plants globally. Alongside these giants, other notable names like Baosteel and US Steel play key supporting roles, each contributing uniquely to the industry's landscape. The vast network of these landmarks forms not only a testament to human achievement but a foundation for future innovations yet to dawn.
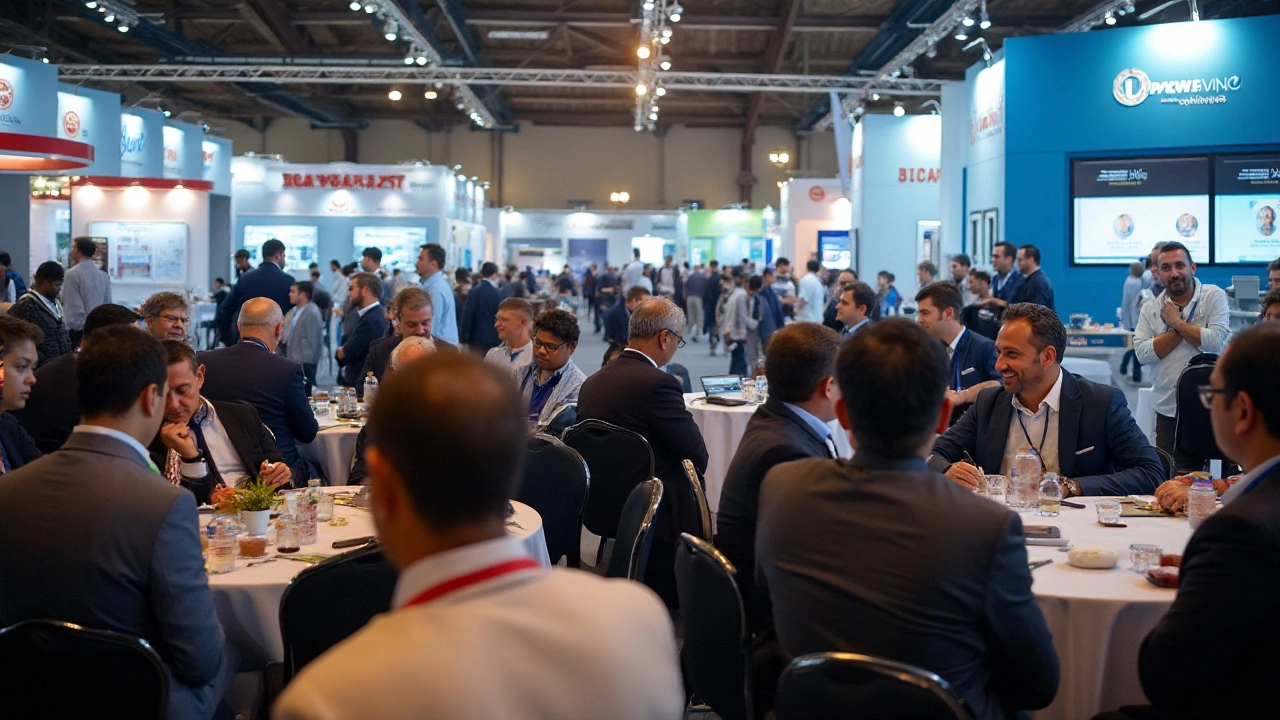
Innovative Techniques and Technologies
The realm of steel manufacturing is constantly evolving, driven by the pursuit of better quality and more efficient processing methods. At the heart of these advancements are innovative techniques and cutting-edge technologies that revolutionize how high-quality steel is produced. Companies are investing heavily in research and development to fine-tune their processes, ensuring they meet the rising standards demanded by various industries worldwide. From the adoption of advanced metallurgy to AI-driven automation, these innovations are reshaping the landscape of steel production.
One of the standout innovations in recent years has been the implementation of Electric Arc Furnace (EAF) technology. This approach has gained popularity due to its versatility and environmental benefits, allowing manufacturers to produce steel with lower carbon emissions compared to traditional blast furnaces. EAF technology utilizes recycled steel, melting it down using electrical energy, which significantly reduces the need for raw material and lessens the environmental impact. This sustainable method has positioned companies that adopt it at the forefront of the industry, aligning with global efforts to minimize ecological footprints.
In the pursuit of efficiency and precision, many leading manufacturers are employing machine learning algorithms and AI systems to optimize their production lines. These intelligent systems can predict equipment failures before they occur, thereby minimizing downtime and maximizing output. By continuously analyzing patterns and anomalies, AI can enhance the quality control process, ensuring every batch of steel meets exacting standards. This application of technology not only boosts productivity but also translates to significant cost savings for companies worldwide.
An industry trend worth noting is the integration of Industry 4.0 principles. These involve the digitalization of manufacturing systems where IoT devices feed data in real-time to centralized control systems. This data-driven approach facilitates more precise control over the myriad variables in the production process. The processing facilities now resemble high-tech labs more than the industrial plants of the past. According to a recent
Steel Manufacturers Association report, the adoption of Industry 4.0 has decreased error rates by 20% across participants in their survey.
Adapting to these new technologies requires a skilled workforce, which has led to a surge in specialized training programs. These programs are essential for workers to operate sophisticated machinery and software platforms driving modern manufacturing lines. Educational institutions are stepping up to collaborate with industry leaders, ensuring the next generation of employees is equipped with the necessary skills to navigate this tech-driven landscape.
Despite the advances, challenges remain. The high investment needed for deploying these technologies poses a barrier for smaller enterprises. Additionally, the rapid pace of innovation requires ongoing adaptation, and companies must stay agile to remain competitive. Yet, embracing these technologies can yield substantial rewards, setting the path for those seeking to lead in quality and efficiency in steel manufacturing in the coming years.
Environmental and Sustainability Efforts
In recent years, the steel industry has witnessed a growing focus on environmental and sustainability efforts. As global awareness around climate change and environmental deterioration intensifies, leading steel manufacturers are making significant strides towards reducing their environmental footprint. This transformation is essential not just for regulatory compliance but for shaping a sustainable future. The industry, once a major contributor to carbon emissions, is reimagining itself through innovative practices that minimize its ecological impact while maintaining the high steel quality that is crucial for technological and infrastructural advancements.
Large players in the steel industry are increasingly investing in technologies designed to lower emissions and reduce waste. A prominent example is the adoption of electric arc furnaces (EAF), which use recycled scrap steel and result in substantially fewer emissions compared to traditional blast furnaces. Companies like ArcelorMittal are at the forefront, having pledged significant reductions in CO2 emissions, supported by investments in hydrogen-based steelmaking processes and carbon capture technologies. These measures enable the use of alternative fuels and the storage of emissions, contributing to cleaner production chains.
The Role of Recycling
Recycling remains a core component of sustainability strategies within steel manufacturing plants. The steel industry boasts one of the highest recycling rates, with modern facilities often achieving upwards of 90% recycled content. This practice not only minimizes waste but also reduces energy usage significantly since recycling steel requires less than 30% of the energy needed to produce new steel from raw materials. As a result, recycled steel is becoming a valuable resource, edging its way into the mainstream manufacturing processes of many leading producers."Sustainability isn’t just a business imperative; it's a moral obligation," remarks the World Steel Association. "The industry's future will hinge on its ability to adapt and innovate to meet the demands of an eco-conscious world."
Adhering to sustainable practices is not a competitive edge but a necessity in today's market. Businesses, governments, and consumers alike demand products that reflect a commitment to the environment. Companies excelling in this area combine innovative techniques with transparency about their supply chains, carbon footprints, and sustainability goals. By prioritizing green philosophies, these manufacturers are not just conserving the planet's resources but are also setting the benchmark for the future direction of the steel industry.

Choosing the Right Steel for Your Needs
Deciding on the perfect type of steel seems daunting with so many options, yet understanding your project demands can make this choice clearer. Begin by considering the environment where the steel will be used, as you may need corrosion-resistant options like stainless steel for humid areas or marine applications. Each type of steel carries its unique characteristics whether it’s tensile strength, hardness, or malleability, and educating yourself on these can spell success or failure for your construction, machine, or appliance.
For instance, carbon steel, which contains a higher amount of carbon, offers strength but lacks corrosion resistance. Stainless steel, on the other hand, includes chromium, thus creating a robust barrier against rust. Where weight is a forefront concern, like in aerospace applications, opting for an alloy with titanium could prove advantageous, providing high strength with minimal mass. Remember, visual aesthetics matter too, especially for projects requiring a polished finish, which chromed or galvanized steel can beautifully deliver.
Cost is undeniably an influential factor. While high-end alloys might boast impressive properties, assessing your budget against these properties can help avoid wastage. Remember, investing in higher quality steel may mitigate long-term expenses like maintenance and replacements. One must take into account the material's ability to be fabricated and formed, which largely influences labor and processing costs. Hot-rolled steel, for instance, is cheaper but less accurate, whereas cold-rolled steel may come at a premium but offers superior precision and finish.
"The foundation of quality is choosing the right materials that fit both the project's specifications and budget," says John Parker, CEO of a renowned construction firm.
Understanding Steel Grades and Standards
Familiarity with the grading system is pivotal. For example, AISI grades steel based on carbon content and alloying elements, hinting at the suitability for different kinds of applications. ASTM and SAE offer standards that ensure uniformity and quality assurances across industries. Cross-referencing your requirements with these standards can be the difference between operational efficiency and continual setbacks.Let's unwrap a common scenario in construction: building with structural steel like A36, which features a balanced blend of ductility and strength and is a go-to in building frames. You would weigh this against options like A572, which can offer higher strength per unit weight and might be the smarter pick when supporting larger loads. It’s about striking a harmony between application needs, material properties, and economic feasibility.
Hands-On Testing and Consulting Experts
Never underestimate the significance of consulting with materials specialists. These professionals can conduct hands-on tests to ascertain durability and performance under simulated conditions, providing insights a mere datasheet might not reveal. For a thoroughly informed decision, industrial experts advise amalgamating these consultations with the technical specifications to nourish your understanding.If the decision feels overwhelming, break down the requirements of your task. Consider reading unbiased reviews and seeking feedback from peers or industry forums may highlight practical experiences, pros, and cons pertinent to the steel quality you explore. Undoubtedly, the right choice will propel project efficiency, safety, and longevity.