Steel has long been a staple in construction and industry due to its strength, versatility, and cost-effectiveness. With the rapid progression of technology and increasing focus on sustainability, the steel industry finds itself at a crossroads. Today, innovations are reshaping how we use steel, presenting new opportunities and challenges.
The future of steel involves not just refining traditional methods but also integrating cutting-edge technologies that enhance its properties and applications. This journey not only addresses economic concerns but also aligns with environmental goals. Understanding these shifts is crucial for stakeholders looking to stay ahead in the evolving landscape of global manufacturing.
- The Role of Steel in Modern Industry
- Current Innovations in Steel Manufacturing
- Future Trends and Predictions
- Sustainability and Eco-Friendly Practices
- Impact on the Global Market
The Role of Steel in Modern Industry
Steel is more than just a metal; it's the backbone of modern industry and a crucial element that supports a myriad of structures and products. Its applications range widely from towering skyscrapers and expansive bridges to the intricacies of modern electronics and transportation. Across the globe, steel stands as a cornerstone of industrial prowess, playing a critical role in infrastructural development and technological advancements. Its unique combination of strength, malleability, and cost-effectiveness enables it to be used in endless innovations and constructions.
The adaptability of steel allows it to evolve alongside technological advancements. For instance, the automotive industry heavily relies on steel for its reliability and energy absorption capabilities in safety designs, ensuring modern vehicles meet regulatory standards while maintaining aesthetic appeal. Steel manufacturing has become an integral part of producing lighter vehicles, which helps in achieving better fuel efficiency and reducing emissions.
According to the World Steel Association, in 2023, global steel production reached approximately 1,800 million tonnes. This staggering number underscores its vast presence and indispensability in contemporary production industries. Manufacturing processes such as electric arc furnaces (EAFs) have significantly optimized energy consumption, showcasing the innovative leaps within the industry.
"Steel's versatility and sustainability make it an ideal candidate for the evolving demands of modern-day production, driving industries toward a greener future," stated Michael Walsh, a renowned materials expert.
Moreover, the shift towards digital manufacturing with AI and IoT integration is revolutionizing steel production plants, making them smarter and more responsive to market needs. Steel manufacturing facilities now feature more advanced automation systems that handle everything from quality control to equipment maintenance, ensuring efficiency and precision in production. This modernization not only speeds up manufacturing but also cuts costs and reduces wastage, aiding sustainability efforts.
The construction industry, too, owes much to steel, where it has long been prized for its incredible strength-to-weight ratio. Innovations in modular construction and prefabrication have embraced steel as a primary material, allowing for quicker assembly times and reduced on-site labor. These advancements are pivotal in addressing housing shortages and infrastructure needs in rapidly urbanizing regions worldwide.
Current Innovations in Steel Manufacturing
As the backbone of modern infrastructure, steel manufacturing is a field continually on the brink of innovation. Today, we witness ground-breaking transformations that promise to revolutionize the industry. One exciting advancement is the implementation of steel that is both lighter and stronger. Researchers have developed alloys that incorporate a mix of vanadium and titanium, giving birth to super-strong yet lightweight materials. These innovations are not just theoretical; they are setting a new standard in sectors ranging from automotive to aerospace industries. Such alloys reduce the weight of cars and aircraft, improving fuel efficiency and performance large-scale.
Within the realm of innovative manufacturing, digitalization takes center stage. Adopting technology like the Internet of Things (IoT) and artificial intelligence (AI) allows plants to optimize processes and reduce waste significantly. Technologies enabling the collection and analysis of real-time data help manufacturers anticipate equipment failures, thus minimizing downtime. As a result, the precise monitoring of production reduces raw material consumption and improves energy efficiency, addressing both economic and environmental concerns. This shift towards smart manufacturing represents a critical leap toward a sustainable future for steel production.
Another major trend reshaping the landscape is 3D printing or additive manufacturing. This technology has opened up new possibilities for customizing steel parts in previously unachievable ways. By layering material precisely, it reduces waste production, offering more eco-friendly solutions compared to traditional subtractive methods. Industries such as aerospace and medical fields are particularly excited about these developments, as they see a future where bespoke solutions offer a competitive edge and foster greener practices. The increased flexibility in design and production also means shorter lead times and fewer transportation emissions, further supporting sustainability goals.
'Innovation in steel is not just a possibility but a necessity. As we push the boundaries of what's possible, new alloys and manufacturing techniques stand ready to shape our future.' - Dr. Helena Roberts, Steel Industry Specialist.
Sustainability also extends into recycling, a core component of innovation in steel manufacturing. Modern facilities are now equipped to recycle steel with unprecedented efficiency, often incorporating more than 90% recycled content into new products. By adopting advanced sorting technologies, we have managed to streamline the recovery process of valuable materials. This breakthrough is transforming waste into a resource, significantly reducing the industry's carbon footprint. The environmental benefits are profound, as recycling uses substantially less energy than producing steel from raw materials.
Lastly, global collaboration and partnerships play a pivotal role in advancing steel innovations. Corporations and research institutions around the world are collaborating to develop new technologies and share best practices. This helps in addressing common challenges like reducing CO2 emissions and improving resource efficiency. These partnerships foster an environment of shared learning and innovation, encouraging a more interconnected and sustainable industry. As these innovations continue to mature, the future of steel manufacturing looks promising, aligning with the modern demands of a greener, more efficient world.
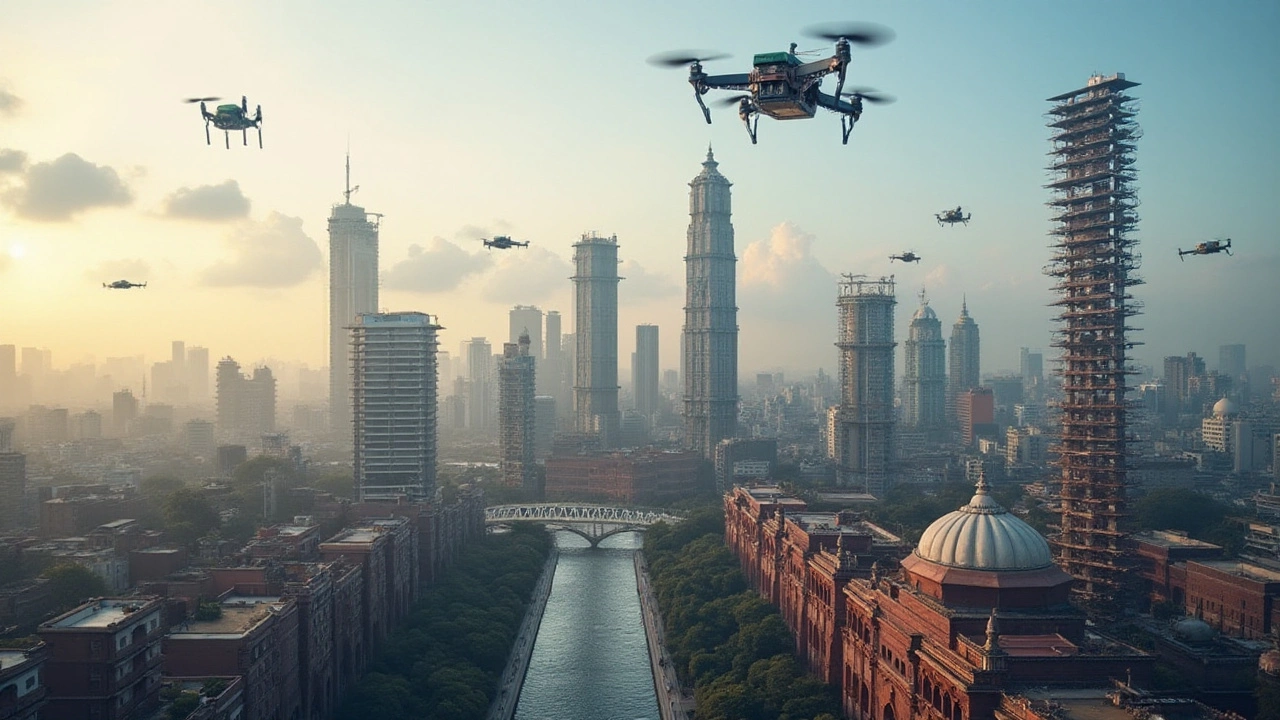
Future Trends and Predictions
The future landscape of steel manufacturing is poised to undergo transformative changes, driven by the increasing need for efficiency and sustainability. As we march into a new era of technological advancements, several promising trends are taking shape, each offering a glimpse into how the industry might look a decade from now. A pivotal trend is the adoption of smart manufacturing technologies, which include AI and IoT systems. These technologies allow for real-time data collection and analysis, streamlining production processes to reduce waste and energy consumption.
Another significant focus area is the development of lightweight, high-strength alloys. These materials, often incorporating elements like aluminum and titanium, are engineered to improve performance while minimizing material use. Automakers and aerospace industries, in particular, have shown keen interest due to the pressing need for fuel efficiency and sustainability. An emerging method, known as additive manufacturing—colloquially referred to as 3D printing—is set to revolutionize how steel is processed and used, enabling unparalleled design flexibility and resource optimization.
A growing emphasis on sustainability is reshaping every aspect of production, with strategies such as electrification of steel plants to reduce carbon footprints. Sweden's HYBRIT project exemplifies this push toward green manufacturing, as it aims to produce fossil-free steel by utilizing hydrogen instead of coal as a reducing agent. This pioneering approach could potentially lower global CO2 emissions from the steel industry by around 35%.
"The future of the steel industry will be defined by its ability to innovate and adapt to environmental pressures," notes Dr. Hans Jürgen Kerkhoff, President of the German Steel Federation.
Meanwhile, markets are expanding for recycled steel materials, driven by both regulatory pressures and consumer demand for sustainable products. Companies are investing in technologies that enhance the quality and efficiency of recycling processes, helping to meet both economic and environmental targets. In parallel, geopolitical shifts and trade policies continue to influence global dynamics, requiring manufacturers to be agile and responsive to changing regulations.
Embracing Digital Transformation
Digital transformation within the steel industry is another key trend, involving everything from supply chain optimization to advanced analytics. Predictive maintenance powered by AI helps manufacturers preempt machine failures, enhancing industry reliability. This shift not only reduces costs but also increases output, making it an asset in a highly competitive global market. According to a recent survey, about 70% of steel-makers plan to increase their AI investments in the coming years, signaling a strong shift towards analytics-driven processes.
With innovations constantly emerging, the future of steel manufacturing presents a challenging yet exciting frontier. As key players continue to explore new technologies and sustainable practices, the traditional boundaries of the industry are expanding, inviting novel applications and possibilities across various sectors. Embracing these changes is crucial, as those who adapt effectively will not only thrive amidst these challenges but will also set new standards for the industry at large.
Sustainability and Eco-Friendly Practices
As industries worldwide ambitiously steer towards greener operations, the steel manufacturing sector is no exception. Significant emphasis is now placed on adopting sustainable practices that not only minimize the environmental impact but also reduce the carbon footprint associated with traditional steel production. The future metal innovations in this area are promising, with increased research focused on reducing emissions and energy consumption. Incorporating technologies such as carbon capture and storage, energy recovery, and eco-friendly raw materials, companies are making notable strides.
Many steel manufacturers have started implementing electric arc furnaces, which are more eco-friendly than conventional blast furnaces, as they recycle steel scrap and use less energy. This innovation not only conserves raw materials but also greatly reduces waste and associated pollution. Additionally, green hydrogen is emerging as a clean energy source in production processes, aiming to replace the carbon-heavy coke traditionally used. This transition to cleaner energy sources could potentially reshape the industry's carbon emissions profile.
The industry is also exploring the potential of digitally transforming manufacturing processes. Utilizing digital twin technology, for example, allows for the simulation and optimization of production facilities. These digital systems can identify areas for improvement, enhancing efficiency and sustainability. The adoption of these practices reflects an overarching trend where technological advancements are steering industries toward more sustainable operations. According to Dr. Varga, a noted industry expert, "The commitment to sustainability is no longer optional but a necessary evolution for survival and prosperity."
Beyond technological innovation, there is a growing movement to incorporate recycling within the steel industry. By recycling steel products at the end of their life cycle, manufacturers can save up to 74% of the energy required for producing new steel. This practice not only conserves resources but significantly reduces greenhouses gases emitted during production. Interestingly, steel is one of the most recycled materials globally, with a recycling rate exceeding 85% in many areas, which greatly supports circular economy objectives.
Moving ahead, policy changes and regulatory frameworks also play a crucial role in driving the adoption of eco-friendly practices. Governments globally are setting stringent targets for emissions reductions and encouraging sustainable industrial practices through tax breaks and subsidies. Such measures are essential in encouraging both small and large players in the market to transition toward greener methodologies. As consumer awareness and demand for sustainability grow, companies that have integrated comprehensive eco-friendly strategies are likely to see a competitive advantage.
Moreover, sustainability within steel manufacturing isn't purely environmental. It's about fostering community involvement and socio-economic development too. Companies are now exploring programs that promote local employment, fair-trade practices, and community investments. This holistic approach to sustainability ensures long-term viability, aligning business goals with broader societal expectations.
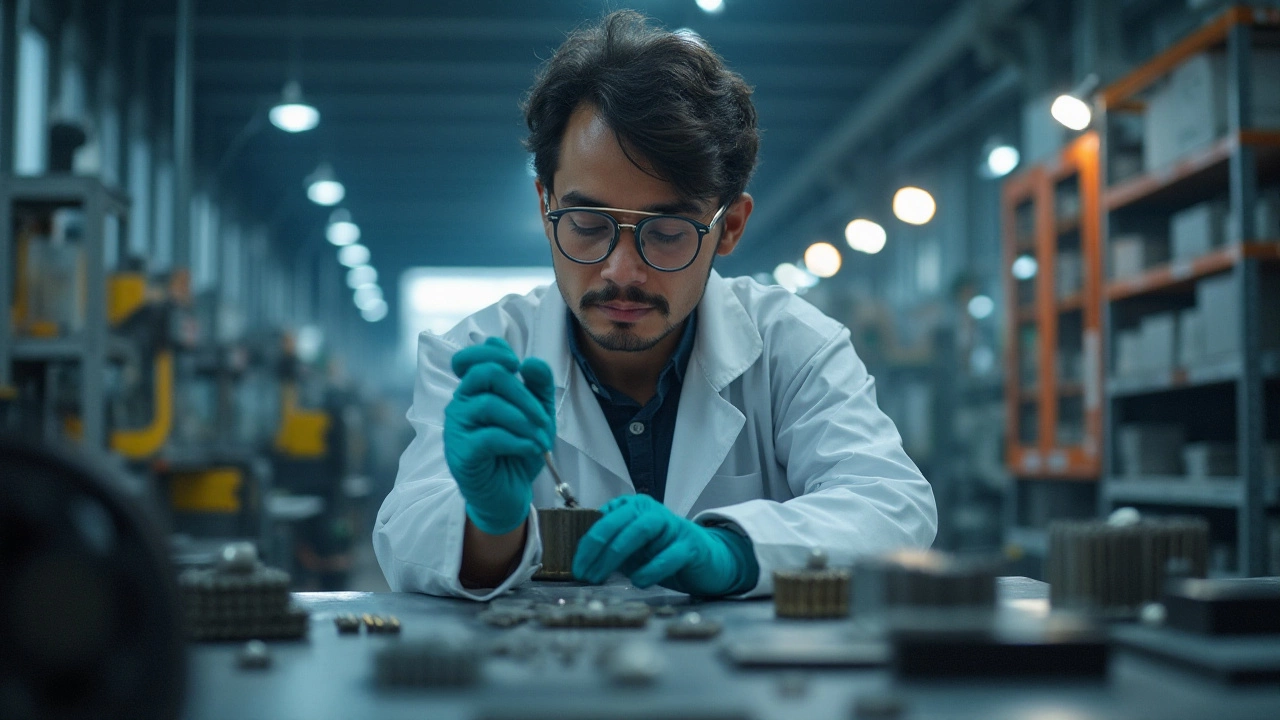
Impact on the Global Market
The evolution of the steel industry is profoundly altering the dynamics of the global market, creating rippling effects across various sectors. Today, steel remains a critical driver of global economic health, underscored by its integral role in infrastructure, automotive, and appliance manufacturing. As countries scramble to modernize their infrastructure, the demand aperture for quality, sustainable steel broadens, influencing global trade patterns. China, as the world's largest steel producer and consumer, wields significant influence in setting global steel prices. Its economic policies can cause fluctuations that impact countries worldwide, often dictating the terms of international trade agreements.
Global trade tensions, sometimes impacting steel tariffs, often challenge the market stability. For example, the US-China trade war led to significant shifts in steel price patterns and trading partnerships. Countries like India and Vietnam have started emerging as critical players in the steel manufacturing landscape, fueled by rapid industrialization and infrastructure expansion. This gradual shift highlights a diversification of the global steel supply chain, creating both opportunities and risks for traditional steel giants. Post-COVID recovery has expedited this growth, emphasizing the demand for innovative steel types, including high-strength and lightweight variants to meet modern needs.
"The steel industry is not just evolving; it is redefining itself in the global landscape," explains John Ferriola, former CEO of Nucor Corporation, highlighting the transformative phase that the industry is experiencing.
Environmental regulations are another pivotal factor reshaping the steel industry's global impact. Countries across Europe and North America are leading the charge towards greener manufacturing processes, prompting steel companies to innovate rapidly. The shift towards electric arc furnace technology, which is less carbon-intensive than traditional methods, embodies this push towards sustainability. As a result, companies that quickly adapt to these innovations can gain a competitive edge, attracting investment and favorable trade conditions. This evolution is not restricted to developed nations; developing countries are also recognizing the economic benefits of sustainable practices, opening new markets for eco-friendly steel products.
The rise of automation and digital technologies such as AI and IoT in steel manufacturing is another aspect influencing the global market. These technologies enhance production efficiency and reduce costs, which is crucial for maintaining competitiveness in international markets. The embrace of technology is nurturing a new era of precision and efficiency, allowing manufacturers to meet the increasingly sophisticated demands of consumers and governments alike. Initiatives that merge AI with traditional practices foresee a future where steel is not only resilient and affordable but also intelligent, enabling smart infrastructure and products.