Plastics are everywhere, and that's not just a thing of modern life—it's a business opportunity. If you're diving into the world of manufacturing, or you're just curious about what makes some types of plastics more popular than others, you've come to the right spot. Let's talk plastics, more specifically, the ones that are making waves in the industry right now.
Ever heard of polyethylene? It's one of those unsung heroes in the world of plastics. This stuff is incredibly versatile, used in everything from shopping bags to bottles, and it's popularity just keeps soaring. Why? Mainly because it's both durable and cost-effective, making it a favorite among manufacturers.
- Introduction to Plastic Demand
- Polyethylene's Popularity
- Role of Polypropylene
- ABS and Its Applications
- Sustainability and Biodegradable Options
- Tips for Aligning Production
Introduction to Plastic Demand
It's no secret that plastics play a major role in manufacturing today. But why exactly is plastic demand skyrocketing? It's all about versatility and adaptability. Plastics aren't just about packaging anymore; they're fundamental in automotive, construction, and electronics industries. Their unique characteristics, like being lightweight and durable, make them ideal substitutes for materials that are heavier and more expensive.
Now, let's break it down even further. A big reason for plastic's popularity is its cost-effectiveness. With manufacturing companies always looking to cut expenses, plastics provide a cheaper alternative without compromising on quality. They've become essential in creating products that are not only lightweight but also maintain a high standard of durability.
Technology Driving Demand
As tech evolves, so does the demand for innovative materials. Today, engineers and designers push for plastics that can do more—think heat resistance or enhanced flexibility. The rise of 3D printing further fuels this, needing plastics that are easy to model and mold.
Environmental Concerns
While demand for plastic types like polyethylene and polypropylene remains high, there's also a growing focus on sustainability. Consumers care more about what happens to their products at the end of life. Companies are responding by developing biodegradable plastics. This shift not only satisfies eco-conscious consumers but also defines future market trends.
In 2023, the global demand for plastics reached peak levels, hitting over 400 million tons. Countries leading the charge include China and the US, showcasing the universal need for these materials in production lines worldwide.
Country | Plastic Consumption (Tons) |
---|---|
China | 120 million |
United States | 50 million |
India | 18 million | Germany | 14 million |
Polyethylene's Popularity
Polyethylene is like that friendly neighbor who’s always around and somehow helps everyone. This plastic has truly made its mark due to its unmatched versatility and low cost. If you pick up a shopping bag, chances are, it's polyethylene. It's the king when it comes to everyday plastic usage, largely due to its capacity to be molded into just about anything.
There are two main types of polyethylene: Low-Density Polyethylene (LDPE) and High-Density Polyethylene (HDPE). LDPE is more flexible, perfect for those squeezy bottles and plastic films, while HDPE is sturdier and used in products like hard containers and tanks.
According to Plastic Today, 'Polyethylene remains the world’s most produced plastic with global production exceeding 100 million tons annually.'
One reason for its continued dominance is its production simplicity and recyclability. More and more manufacturers are looking at eco-friendly options, and polyethylene offers some breathing room since it can be recycled relatively easily compared to other plastics.
Why Manufacturers Love It
- Cost-Effective: Its affordability makes it ideal for mass production.
- Lightweight: Helps in reducing shipping costs due to its minimal weight.
- Easy to Process: It can be shaped, cut, and assembled with ease.
- Recyclable: Contributes to circular economy efforts, making it a hit in sustainability discussions.
The versatility of polyethylene means its applications are only limited by imagination. From construction to packaging, its demand is still strong and growing. If you’re in the manufacturing sector, keeping an eye on polyethylene trends might just keep you ahead of the curve.
Role of Polypropylene
Polypropylene, sometimes referred to as PP, is no joke in the plastic manufacturing game. It's like the Swiss Army knife of plastics—it does a little bit of everything. Common wherever you look, from the packaging around your new gadgets to the bumper on your car, PP takes versatility to a whole new level.
Why Is Polypropylene Popular?
This plastic is loved for its durability, which makes it perfect for heavy-duty applications. It's got a high melting point, so it holds up well in thermal stress—imagine your microwave-safe containers—that's usually polypropylene doing its thing.
The material is also relatively cheap compared to some other plastics, making it pretty attractive for large-scale use. It's tough, flexible, and lightweight, all while being surprisingly resistant to different chemical solvents, acids, and bases.
Where Do You Find It?
PP is the go-to material for a wide range of products:
- Food containers you use daily.
- The dashboards in vehicles.
- Ropes and carpets.
- Even banknotes in some countries.
Another fun fact? It's used in piping systems, thanks to its excellent resistance to abrasion.
Environmental Considerations
Polypropylene isn't all sunshine and rainbows. Like other plastics, it's tied to environmental concerns. Recycling PP can be a bit tricky, but the demand for recycled polypropylene is on the rise. Initiatives to make PP more eco-friendly are gaining momentum, with a focus on improving recyclability and reducing carbon footprints.
As more companies hop on the sustainability bandwagon, the hope is that PP will become even more environmentally responsible. Whether you're in the business or just an eco-conscious consumer, keeping an eye on these trends can be worth your while.
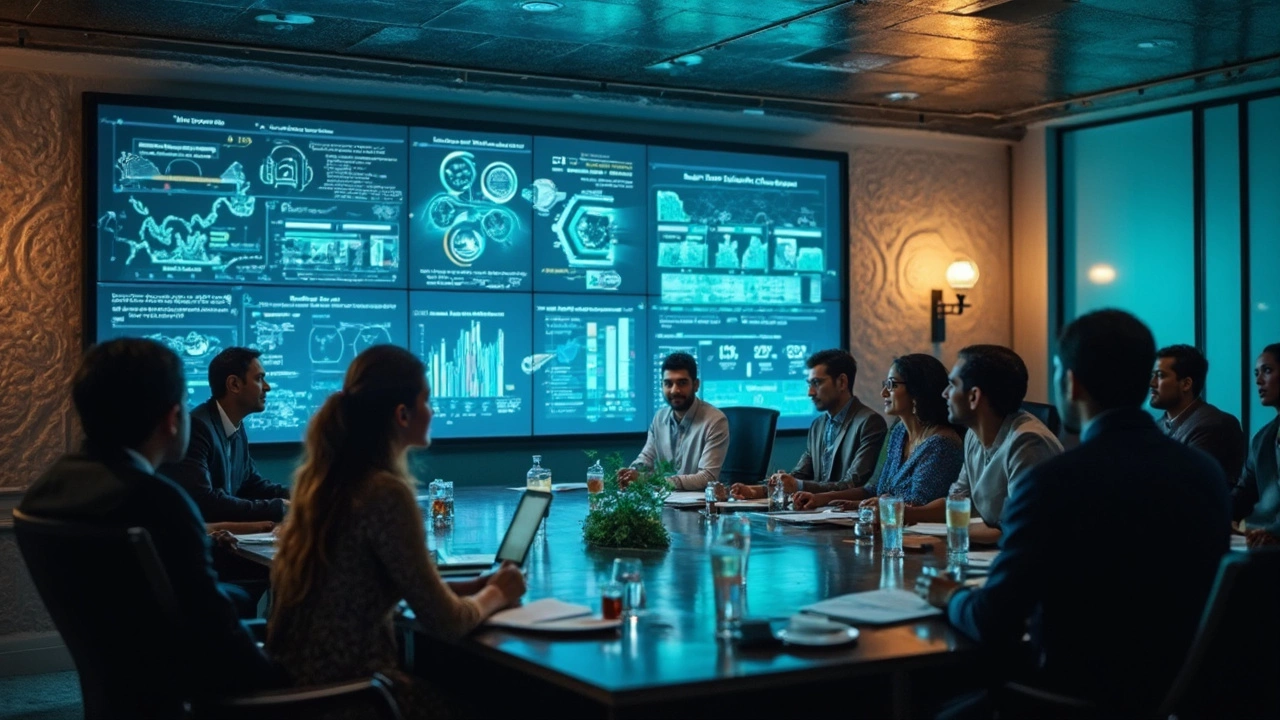
ABS and Its Applications
When it comes to durable and reliable plastics, ABS, or Acrylonitrile Butadiene Styrene, definitely deserves a mention. This thermoplastic is well-known for its toughness and impact resistance, making it a go-to choice in multiple manufacturing sectors.
ABS is often seen in everyday products that need durability and strength. Think about LEGO bricks or some of your car parts. Yup, they're probably made of ABS. Its ability to withstand physical impacts without cracking is what makes it valuable. Plus, it can resist a fair amount of heat, which isn't something every plastic can brag about.
Versatile Uses
You'll find ABS in plastic manufacturing industries, especially when producing items that require robust performance. It's used in electrical enclosures, consumer electronics, and even in piping systems. Why is it used so widely? Simplicity in molding combined with excellent mechanical properties!
Why Manufacturers Love ABS
Besides durability, manufacturers favor ABS because it can be easily machined, sanded, or glued. That means it's also popular in 3D printing, allowing designers to prototype quickly. Also, it handles color pigmentation exceptionally well, so products don't just perform well—they look great too!
Safety and Sustainability
Environmentally speaking, ABS is considered relatively safe because it doesn't have known carcinogens. However, it's not biodegradable, and recycling can be a bit tricky due to its complex structure. Still, enhancements and innovations in recycling methods are gradually making the process easier.
Property | Value |
---|---|
Density | 1.04 g/cm3 |
Melting Point | >105°C |
UV Resistance | Low |
So there you have it. Whether you're in the industry or just a curious mind, knowing where ABS fits in the world of plastic demand gives insight into its multitude of applications.
Sustainability and Biodegradable Options
As our planet cries out for more eco-friendly practices, the demand for sustainability and biodegradable plastics has seen a significant uptick. It's no wonder companies big and small are rolling up their sleeves to incorporate these alternatives into their manufacturing processes.
Bioplastics Rising
Here comes the knight in shining armor: bioplastics. Made from natural materials like corn starch and sugarcane, these plastics are a hit for those aiming to go green. They have the potential to reduce carbon footprints significantly. Plus, they're a renewable source, unlike their petroleum-based cousins, making them a favorite in the new green rush.PLA and PHA: The Stars
PLA (Polylactic Acid) and PHA (Polyhydroxyalkanoates) are leading the charge. PLA is super popular for 3D printing, offering a fantastic option for prototypes and products that need a biodegradable touch. PHA, on the other hand, is like the Swiss Army knife of bioplastics—used in anything from packaging to medical applications. They're both biodegradable, echoing the market trends towards responsible production.Environmental Considerations
Pushing toward sustainability isn't just about materials. It's also about energy-efficient production processes. Smart manufacturers are embracing renewable energy sources and closing the loop with recycling strategies that bring used plastics back to life.Cost vs. Benefit
Factor | Traditional Plastics | Biodegradable Plastics |
---|---|---|
Cost | Lower | Higher |
Environmental Impact | High | Low |
Popularity | High | Growing |
So, if you're in the manufacturing game, it's time to consider these alternatives seriously. Not only could they help your business align with plastic market trends, but they also offer a way to make a positive impact on the planet.
Tips for Aligning Production
Aligning your production with current plastic demand isn't just about staying trendy; it's about making smart business moves. Here's how you can keep up with what's in demand and ensure you're not left behind.
Understand Market Trends
Keeping your ear to the ground is crucial. Before diving into production, research which types of plastics are in demand. Look at market reports and case studies. Knowing that polyethylene is a bestselling choice, for instance, can help you plan better.
Focus on Sustainability
With more companies shifting to eco-friendly practices, incorporating sustainable plastics can give you a competitive edge. Biodegradable options are gaining popularity, especially with increasing environmental awareness among consumers.
Optimize Production Processes
Efficiency never goes out of style. Analyze your production processes and see where you can cut waste or speed things up without sacrificing quality. This is particularly crucial if you're dealing with high-demand plastics like polypropylene, which is favored for its strength and versatility.
- Keep machinery updated and well-maintained.
- Train staff regularly on the latest technologies.
- Use data analytics to forecast demand changes.
Collaborate and Network
Sometimes, letting others help can propel you forward. Work with suppliers and other industry players to exchange insights on what's working and what's not. Collaboration can offer new perspectives and opportunities.
Invest in Quality Control
Demand is great, but only if you're meeting quality expectations. Invest in robust quality control processes to ensure your products don't just reach the market but make a good impression.
By taking a strategic approach and aligning with these steps, your plastic manufacturing business can not only meet current demands but also be ready for whatever the market throws its way.