The U.S. manufacturing sector serves as a backbone to the nation’s economy, with factories and production lines pulsating at the heart of industrial growth. In 2025, this sector stands at a crossroads, with factors like government policies, innovation, and globalization playing significant roles in its trajectory.
Understanding the historical context of American manufacturing is crucial to appreciating its current state. Through the peaks and valleys of industrial changes, new government initiatives have emerged in recent years, aiming to rejuvenate and boost industrial activities across various states.
Technology remains a pivotal player, transforming production methods and capabilities. However, growth does not come without obstacles. Manufacturers today face several challenges, from global competition to supply chain intricacies, each demanding strategic responses.
Despite these hurdles, there have been notable success stories of companies adapting and thriving, shedding light on strategies that work. This leads us to consider future trends—what's next for U.S. manufacturing? Only time will tell how these dynamics unfold, but informed insights can guide stakeholders through the journey.
- Historical Context of U.S. Manufacturing
- Recent Government Initiatives to Boost Manufacturing
- Technological Innovations and Their Impact
- Challenges Facing the Manufacturing Sector
- Success Stories: American Manufacturing Revivals
- Future Trends and Predictions for U.S. Manufacturing
Historical Context of U.S. Manufacturing
The story of U.S. manufacturing begins with the early days of the American Industrial Revolution, a period characterized by rapid industrial growth and innovation. In the late 18th and early 19th centuries, American factories started adopting mechanized systems pioneered by the British, leading to increased production efficiency. During this transformative era, key inventions such as the cotton gin and interchangeable parts revolutionized industries, setting a precedent for modern manufacturing practices. These innovations not only contributed to the rise of industrial giants but also laid the groundwork for economic expansion, as America evolved from an agrarian society to a burgeoning industrial powerhouse. The foundation of this era was laid with a spirit of ingenuity and enterprise, hallmark traits that continue to define the country’s industrial landscape.
As the 20th century progressed, U.S. manufacturing experienced several shifts, particularly during and after the World Wars. The demand for military supplies catalyzed unprecedented production capabilities, and factories reinvented themselves almost overnight to meet the needs of wartime efforts. This ability to adapt and innovate under pressure showcased the resilience of American manufacturing firms. The post-war period heralded a golden age for U.S. manufacturing, as consumer demand soared, resulting in the proliferation of automobiles, household appliances, and electronics. It was a time when American manufacturing prowess was unparalleled, and "Made in America" became a symbol of quality and reliability worldwide.
However, the latter half of the 20th century saw challenges that tested the resilience of U.S. manufacturing. The oil crisis of the 1970s, combined with rising labor costs and increased global competition, intensified the challenges faced by domestic manufacturers. Particularly noteworthy was the rise of manufacturing hubs in Asia, where lower costs and efficient logistics began to lure American companies overseas. This marked the beginning of a complex era characterized by outsourcing and loss of manufacturing jobs domestically, sparking debates about economic policy and competitive strategies. A well-cited report by the National Association of Manufacturers from the early 2000s noted how "innovation and adaptation are crucial for sustaining America’s industrial lead in a rapidly evolving global economy."
Despite these headwinds, certain areas of U.S. manufacturing have shown a capacity for reinvention. The transition towards advanced manufacturing technologies and a renewed focus on sustainability have opened new avenues for growth. The introduction of automation, robotics, and smart manufacturing systems has gradually transformed a sector once known for mass production into one that is increasingly defined by precision, customization, and efficiency. Today, the U.S. manufacturing sector is a complex tapestry interwoven with traditional practices and cutting-edge innovations.
U.S. manufacturing continues to evolve, driven by an intricate blend of historical influences, technological advancements, and strategic policy initiatives. As we look back at its rich history, it becomes evident that the sector has always thrived on innovation and resilience. These attributes remain essential as the industry navigates the challenges and opportunities of the 21st century.
Recent Government Initiatives to Boost Manufacturing
The United States has undertaken significant steps to breathe new life into its manufacturing sector. These efforts are primarily driven by the recognition that a robust manufacturing base is crucial not just for economic growth but also for national security and resilience. Several policy measures have been rolled out in recent years, aimed at tackling various challenges faced by the industry.
A key component of these initiatives has been the introduction of more favorable tax policies designed to incentivize manufacturing activity within the country. Through measures such as tax credits for research and development, and the repatriation of earnings, companies are encouraged to invest more in local manufacturing efforts. The aim is to make domestic production not only competitive internationally but also lucrative for businesses eyeing expansion.
Moreover, the government has placed a heightened emphasis on workforce development as part of its comprehensive strategy. Recognizing the workforce as the backbone of manufacturing prowess, programs like the Workforce Innovation and Opportunity Act (WIOA) have been funded to provide skills training to workers. This is done to equip them with the necessary capabilities to thrive in a high-tech manufacturing environment, transforming what was once considered blue-collar into a tech-savvy, white-collar job market.
In the realm of technology, government support for innovation has seen the backing of high-tech sectors such as semiconductor manufacturing and AI-driven production processes. Subsidies and grants have been made available to companies engaged in pioneering new technologies. A recent quote from the Secretary of Commerce, "Investing in cutting-edge technology today secures our competitive edge tomorrow," underscores the strategic thrust towards technology-led growth.
Environmental considerations also play a part in the new initiatives. The Manufacturing Leadership Act aims to integrate sustainable practices in production processes, promoting the adoption of green technologies. Manufacturers are encouraged to reduce carbon footprints through incentives linked to sustainable practices, reminding stakeholders that modern manufacturing thrives not just on output but on responsible management of resources.
Another notable initiative is the reshoring effort—bringing back manufacturing operations to American soil. This is driven by the global pandemic's impact on supply chains, highlighting vulnerabilities in depending heavily on international sources. A mix of tariffs on imports and subsidies for local production has become a strategic lever to make American manufacturing more self-reliant.
The Economist recently noted, "The amalgamation of fiscal incentives and strategic policies has put the U.S. manufacturing sector on a path that not just restores its lost glory but adapts it to future challenges."
Government initiatives are, indeed, multifaceted, indicating a commitment to fostering a thriving U.S. manufacturing landscape. By blending traditional manufacturing with new-age exigencies and practices, these initiatives are positioned to drive the sector forward into a new era of growth and innovation.
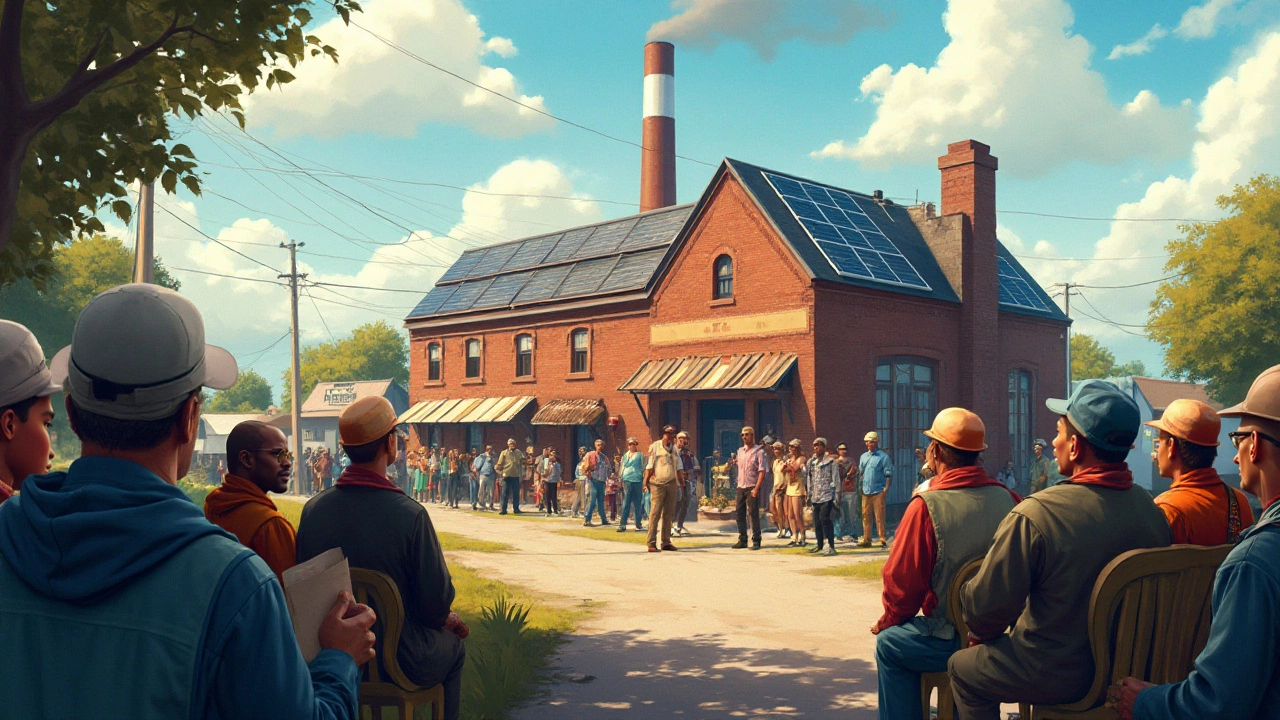
Technological Innovations and Their Impact
In the realm of U.S. manufacturing, technology has consistently been the fire that fuels transformation. The 21st century has seen an explosion of advances, from robotics to artificial intelligence, each redefining how we conceptualize efficiency and productivity in manufacturing. Factories that once hummed with manual labor are now buzzing with automated processes, with machines often lending their precision to tasks once solely performed by skilled hands. The concept of smart manufacturing has emerged, where interconnected systems communicate in real-time, significantly improving decision-making processes. These innovations reduce not only costs but also lead times, making it easier for businesses to compete on a global stage. The widespread use of the Internet of Things (IoT) has further revolutionized the landscape, enabling predictive maintenance, which substantially decreases downtime by troubleshooting issues before they become serious problems.
The impact of technology is palpable, with companies investing billions into digital transformation efforts aimed at gaining a competitive edge. Growth in the sector is propelled by leveraging data analytics to predict market trends and consumer demand with incredible accuracy, enabling manufacturers to optimize production rates accordingly. However, adopting these technologies isn't without its challenges. Companies must navigate the high initial costs of deployment, alongside the continuous upskilling of their workforce to manage these complex systems. In many ways, technology necessitates a change in perspective, moving from a focus solely on production to one that incorporates a broader understanding of market dynamics and consumer behavior. This adaptation process can be daunting; yet, the rewards, including increased agility and responsiveness to market changes, are often worth the effort.
Beyond operational benefits, technological advancements are contributing significantly to sustainability efforts. The fabric of modern manufacturing is interwoven with environmental considerations, where innovations help reduce waste and increase energy efficiency. Automation and advanced data analysis contribute to minimizing emissions and improving resource management. A noteworthy example is the advancement in 3D printing, which not only allows for precise manufacturing but also cuts down material wastage considerably. According to a report by the Department of Energy, industrial energy consumption has decreased by 15% over the past decade, much of which can be attributed to technological innovation.
"Adopting cutting-edge technology isn't just about keeping up—it's about setting the pace for global manufacturing," said Mark Fields, a renowned industry expert in one of his insightful commentaries.
In examining these technological shifts, it's evident that the road to innovation is paved with both challenges and opportunities. As we journey further into this tech-driven era, the U.S. manufacturing sector must remain adaptable, embracing change to harness its full potential. What lies ahead for manufacturers is a continued evolution, as they keep stride with technological advancements that not only promise to improve operational efficacy but also create new possibilities for sustainable growth.
Challenges Facing the Manufacturing Sector
In the current industrial landscape, the U.S. manufacturing sector is not without its set of daunting challenges. A significant hurdle is the intensifying global competition. American manufacturers face relentless pressure from international counterparts, who often operate at lower costs due to cheaper labor and less stringent regulatory environments. This fierce competition from nations like China and Mexico can erode the market share of U.S. firms, compelling them to innovate continuously and streamline operations to stay viable.
The sector is also grappling with the issue of skilled labor shortages. As technology advances, the need for workers adept in digital skills, robotics, and advanced manufacturing processes grows sharply. However, there is a considerable gap between the skills workers possess and the needs of modern manufacturing. This skills mismatch results in a high demand but low supply of qualified technicians, engineers, and operators, posing a significant threat to the growth and sustainment of manufacturing operations across the United States.
Another critical challenge is the disruption of the supply chain, which has been felt acutely in recent years. The COVID-19 pandemic highlighted vulnerabilities in global supply networks, with delays, shortages, and logistical bottlenecks causing severe impacts on production timelines and costs. Manufacturers have been forced to reconsider their supply chain strategies, often looking to diversify suppliers and incorporate more localized sourcing models to enhance resilience.
The issue of regulatory compliance adds another layer of complexity. U.S. manufacturers must navigate a labyrinth of local, state, and federal regulations, covering aspects from environmental standards to labor laws and product safety benchmarks. This regulatory environment, while essential for ensuring ethical and safe operations, often requires significant resources to monitor and maintain compliance, which can be taxing for smaller enterprises.
Technological advancements, while providing opportunities, also impose challenges. Implementing cutting-edge technologies like IoT, AI, and automation requires substantial investment, both financially and in terms of time and training. For many manufacturers, especially those with limited budgets, the initial costs can be prohibitive, even though the long-term benefits may be significant. Balancing these costs with immediate operational needs is a challenge that manufacturers must strategically manage.
According to the National Association of Manufacturers, "The manufacturing sector contributes over 11% to the U.S. economy's GDP, but it faces constraints that could hamper future growth without strategic innovations and adaptations."
Rising operational costs due to energy prices, coupled with environmental sustainability concerns, present ongoing challenges as well. Efforts to transition to more sustainable practices often require advance planning and investment, which can strain existing resources. Manufacturers are increasingly looking at energy-efficient systems and renewable energy sources to mitigate costs while complying with environmental directives.
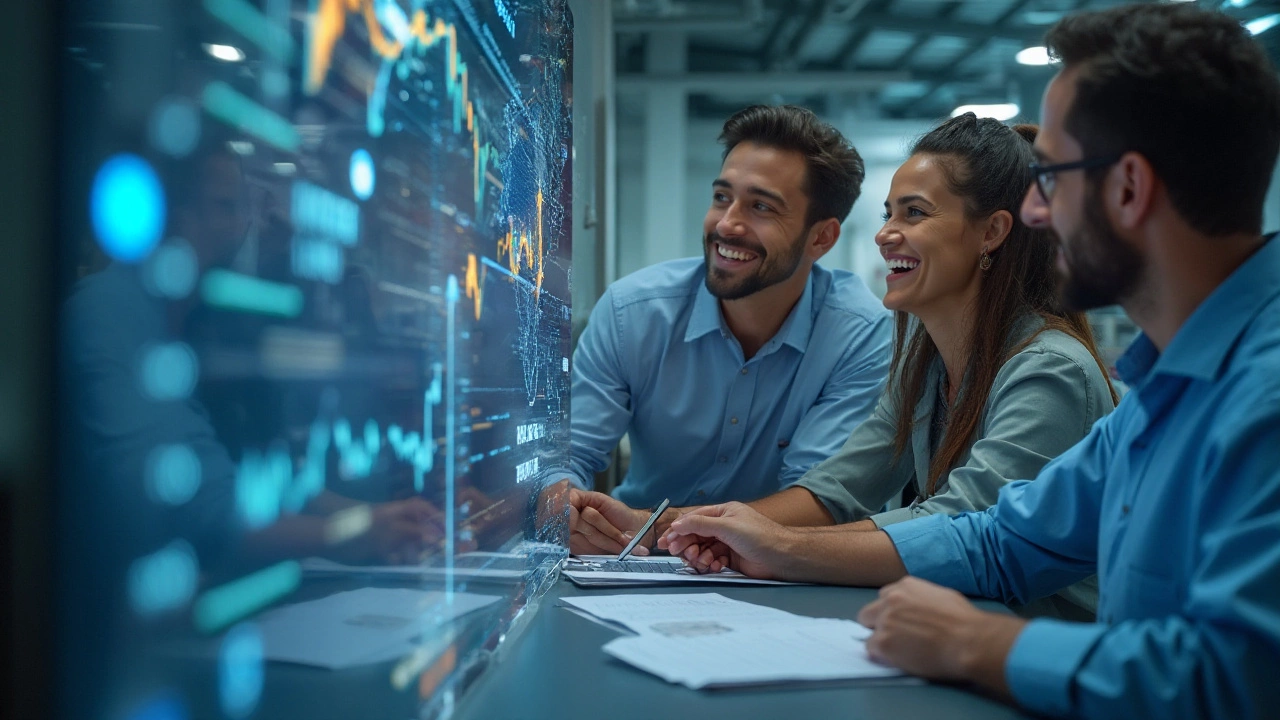
Success Stories: American Manufacturing Revivals
In recent years, the narrative of U.S. manufacturing has begun to shift, with certain regions and sectors demonstrating remarkable resilience and growth. One shining example is the automotive industry in Michigan. Once struggling with the decline of traditional automakers, the state has experienced a revival through strategic investments in electric vehicle production. Companies like Tesla have set the stage for a booming industry, leveraging the government’s clean energy initiatives to retool facilities and create thousands of high-paying jobs. This transition not only rejuvenated the local economy but also placed Michigan at the forefront of future vehicle technology.
Across the country in North Carolina, the biotechnology sector showcases another story of industrial resurgence. The research triangle, comprising Raleigh, Durham, and Chapel Hill, has evolved into a manufacturing powerhouse with tech-driven biopharmaceutical endeavors. It highlights the power of partnerships between universities and private companies in fostering innovation and bringing groundbreaking products to market.
One industry expert remarked, "This is a testament to what can be achieved when industry and academia come together to address real-world challenges."Such collaboration has positioned North Carolina as a magnet for skilled workers and tech investments, resulting in sustained growth and leadership in bio-manufacturing.
The textile industry in South Carolina also stands as a testament to resilience. While many assumed the decline of American textiles was irreversible due to overseas competition, recent developments tell a different story. By adopting advanced manufacturing techniques and focusing on specialty textiles, the industry has carved out a niche for itself. Textiles now include innovative materials such as smart fabrics with integrated sensors, benefiting both the fashion and military sectors. This pivot not only retains jobs but attracts new talent eager to redefine what American textiles can deliver.
The impact of these success stories extends beyond regional economies, influencing national industrial strategies and offering a blueprint for other sectors. For instance, Minnesota’s medical devices industry exemplifies this ripple effect. By fueling manufacturing with advanced robotics and precision engineering, companies have not only enhanced production capacities but also improved product quality and safety standards. Growth in this sector has been significant, positioning the U.S. as a leader in global healthcare solutions.
These revivals in American manufacturing showcase how strategic pivots and embracing technology can effectively rejuvenate industries. They stand as testimonies to the transformative power of federal support, local vision, and innovative thinking. As the nation continues to navigate the complex landscape of manufacturing, these success stories offer valuable lessons in resilience and adaptation for future endeavors.
Future Trends and Predictions for U.S. Manufacturing
The landscape of U.S. manufacturing is constantly evolving, and as we look to the future, several key trends are poised to shape the industry's trajectory. One of the most significant drivers of change is the advancement in automation and AI technologies. These innovations are expected to redefine production processes, increase efficiency, and lower costs across the board. Manufacturers are increasingly adopting smart factories, where machines communicate autonomously, and data-driven decisions enhance productivity. This technological evolution promises a leaner production model tailored to meet the demands of customization and rapid market shifts.
The role of sustainable practices is becoming increasingly vital. Consumers and policymakers alike are emphasizing eco-friendly production, pushing manufacturers to adopt green technologies and energy-efficient systems. Initiatives such as carbon neutrality targets are encouraging factories to reduce emissions and waste. As regulatory frameworks tighten, the transition towards a more sustainable industry is unavoidable. This green revolution offers opportunities to innovate in product design and materials, aligning with global environmental goals.
Another trend gaining momentum is reshoring, where companies bring manufacturing jobs back to the U.S. soil. This movement is fueled by geopolitical tensions, risk mitigation, and the desire to reduce dependency on foreign supply chains. The pandemic amplified vulnerabilities in international logistics, driving the need for localized production. Reshoring not only boosts domestic employment but also strengthens national security by ensuring essential goods are produced locally. However, overcoming cost challenges and finding skilled labor remain hurdles to this transition.
Machine learning is crucial in optimizing the supply chain, forecasting demands, and managing inventories with unprecedented accuracy. By leveraging data analytics, manufacturers can anticipate market needs, reduce stockouts, and minimize excess inventory, enhancing profitability. There's also a growing focus on the circular economy, where products are designed for longevity, repairability, and recycling. This shift not only addresses sustainability but encourages innovation in materials and production techniques.
"With the rapid pace of technological change and geopolitical shifts, U.S. manufacturing is entering a new era of innovation and opportunity," said John Smith, director at the Manufacturing Institute.
To navigate these transformative years ahead, industry players must stay adaptable, embracing change and integrating new technologies strategically. Government incentives and subsidies will play a critical role in facilitating these adjustments, making investments in training and infrastructure crucial. The future of government schemes will likely focus on supporting digital transitions and eco-friendly practices, highlighting the commitment to a competitive and sustainable manufacturing sector. As manufacturers gear up for these changes, they must identify key areas for growth and innovation, ensuring they remain at the forefront of global competition.