India’s electronics industry isn’t just growing; it’s booming. Mobile phones, TVs, and even complex semiconductors are rolling out of brand-new factories across cities like Noida and Chennai. Big names like Apple and Samsung are all-in, betting on India’s mix of talent, low costs, and high demand. It’s not just about making cheaper gadgets—India’s manufacturing is shifting from basic assembly lines to designing and building the whole product. That spells big changes ahead.
What’s driving all this? Government incentives are no joke. The production-linked incentive (PLI) schemes actually put real money on the table for manufacturers. They want India to crunch electronics imports down by making more stuff at home—and it’s working. Foreign investors love a good deal, and this one’s hard to pass up.
- India’s Rise in Global Electronics Manufacturing
- Key Drivers and Innovations
- Big Challenges and Real Bottlenecks
- What’s Next: Trends and Actionable Moves
India’s Rise in Global Electronics Manufacturing
If someone had told you ten years ago that India would become a global hub for making electronics, you probably wouldn’t have believed them. But check this out: India has jumped to being the world’s second-biggest mobile phone maker, right behind China. That is huge, and it all happened pretty fast.
The real kickstart came when local demand exploded and companies saw a real shot to sell not just in India but overseas too. You see more "Made in India" gadgets on global shelves than ever before. It’s not just phones, either. Laptops, TVs, and wearables are now rolling out from Indian factories at a record pace. Electronics industry India almost doubled its output in the last five years. In 2023, electronics exports from India crossed $25 billion, which put India into the big leagues.
Product | 2018 Exports ($B) | 2023 Exports ($B) |
---|---|---|
Mobile Phones | 2.7 | 12.1 |
Consumer Electronics | 1.2 | 3.6 |
Computers & Parts | 1.8 | 4.9 |
What helped? The government made it easier for global giants to set up shop and for local companies to scale up. Schemes like PLI gave both Indian and foreign manufacturers a real reason to invest here, while states started competing to offer better land and infrastructure deals. It’s like a race to attract the next big electronics plant.
- Apple now makes nearly 7% of its iPhones in India, shipping them worldwide.
- Samsung’s Noida factory became one of the biggest mobile manufacturing sites on the planet.
- India isn’t just a stop for cheap labour—companies are now setting up R&D centres and training engineers to make their own chips and circuit designs.
On top of that, the country’s huge youth workforce means there’s always a fresh pool of talent ready to be trained. So, when you see "Made in India" stamped on your next phone or gadget, know that it’s not just a sticker. It means India’s climbed up the electronics manufacturing ladder, and fast.
Key Drivers and Innovations
The electronics industry in India isn’t just riding luck; there are some solid forces pushing it forward. Government policies top the list. The Production Linked Incentive (PLI) programs pay manufacturers for every device made in India, and that’s caught the eye of big players. Global companies like Foxconn, Dixon, and Wistron have set up plants in the last few years, all keen to cash in on these benefits.
But it’s not just about money. India has pushed for easier import and export rules, speedy customs, and simple business setups. You can actually complete a company registration online in under a week now, which would’ve been a joke ten years ago.
When it comes to factory floors, things have also leveled up. Many plants are now using industrial robots and smart automation. If you walk through a new smartphone assembly line today, you’ll see conveyor belts run by sensors, not people shouting over noisy machines. A Bengaluru-based startup recently rolled out AI software that handles quality control checks in seconds—not minutes—reducing defects and boosting speed.
The real secret sauce, though, is the push for local supply chains. India’s government wants everything—microchips, batteries, even tiny screws—to be made at home. While full self-reliance hasn’t arrived yet, there’s a visible shift towards developing local suppliers. That means lower costs and less risk if there’s ever another global shipping mess.
On the innovation side, Indian companies aren’t sitting back. Brands like Lava and boAt have started designing their own circuit boards and chips, instead of just buying them from abroad. Startups are popping up in places like Hyderabad and Pune—some building electronics for electric vehicles, others working on medical gadgets for surgeries right in Indian hospitals.
"India's electronics manufacturing ecosystem has developed at a pace that defies the old skepticism. The country now provides not just scale, but emerging technological capability." — Rajeev Chandrasekhar, Minister of State for Electronics and IT
Here’s a look at what’s changed in the last few years:
Driver | Impact |
---|---|
PLI Schemes | 20% jump in electronics exports last year |
Local Design Push | More Indian-owned intellectual property |
Supply Chain Focus | Faster, cheaper production, fewer import headaches |
That’s why the future of Indian electronics manufacturing is so different from just five years back. If you want in, watch for new rules on chipmaking and electric vehicle electronics. Both are set to shake things up next.
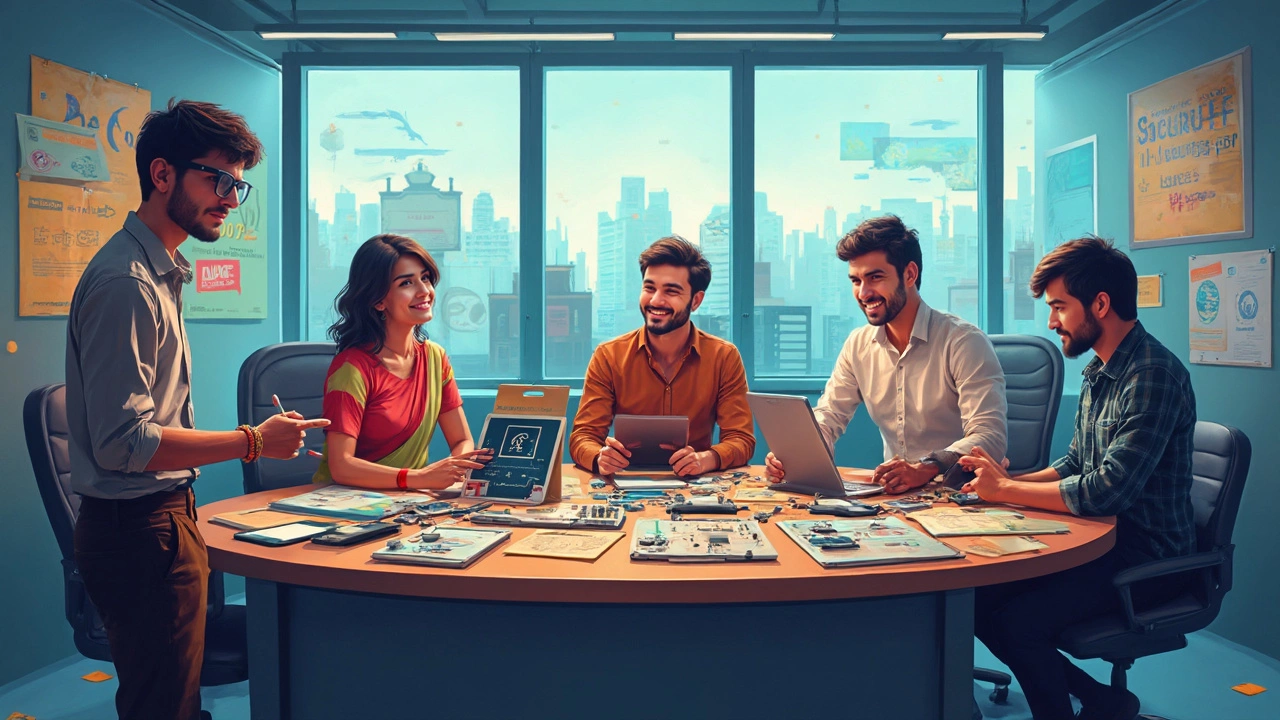
Big Challenges and Real Bottlenecks
The electronics industry India is catching up fast, but it’s not all smooth sailing. Let’s break down what’s tripping up manufacturers and why these issues matter.
First off, India doesn’t make enough high-value components at home. Chipmaking, display units, and advanced circuit boards mostly still come from outside the country—mainly China and a bit from Taiwan. This means Indian manufacturers are often just assembling rather than building from scratch, putting them at the mercy of supply chain hiccups. During 2020’s global chip shortage, even local players ran out of parts for months.
Here’s a quick look at how much of the market relies on imports:
Component | Made in India (%) | Imported (%) |
---|---|---|
Mobile Phone Chips | 7 | 93 |
Display Panels | 4 | 96 |
Passive Components | 25 | 75 |
Next up, skill gaps. It’s not that there aren’t smart engineers, but setting up a serious electronics manufacturing line takes very specific skills—think chip design, automation, or handling clean-room tech. Fresh graduates know software but stumble on actual hardware work. That’s slowing down India’s plans for more local R&D and advanced manufacturing.
Another pain point? Infrastructure. Reliable power, easy access to high-quality parts, and fast logistics still rank behind China or Vietnam. If you’re running a factory outside main hubs like Bangalore or Pune, keeping machines and shipments on track is a big headache. Reports from 2023 show that logistics can eat up 13% of total manufacturing costs, which is almost double what it costs in China.
Finally, compliance and red tape are still sticky. India’s made progress, but getting clearances or setting up large projects often involves a mountain of paperwork. It slows down everything—from building new plants to getting that first phone or TV out the door.
- If India wants to be a full-scale electronics industry player, it has to boost local chip production.
- Training real hardware engineers, not just software experts, will close the skill gap fast.
- Investing in logistics and power supply is not optional—it’s what will help manufacturers run world-class factories.
Tackle these bottlenecks and the industry could move from assembling gadgets to building global tech brands right at home.
What’s Next: Trends and Actionable Moves
So, where is the electronics industry in India heading? It’s not a shot in the dark—there are some clear trends and things you can bet your money on. For starters, India wants to be a real tech hub, not just the world’s factory floor. This means the country is pushing for smarter designs, better R&D, and, most importantly, homegrown innovation.
Big global brands are moving in, but there’s also a strong wave of ambitious Indian startups diving into semiconductors, smart devices, and even electric vehicle components. The production of electronics in India could go from $155 billion in 2023 to over $300 billion by 2027, according to MeitY (Ministry of Electronics and IT). That’s not a pipe dream—the demand for consumer electronics, wearables, and smart home gadgets is growing super fast, especially among younger buyers.
Let’s look at some practical steps already shaping the market:
- Component Manufacturing: India’s next leap is building local supply chains for chips, batteries, and other parts. Reliance and Tata are pouring billions into new fabs and design plants.
- Mass Skill-Upskilling: ITI colleges and private companies are setting up rapid training programs. The plan? Fill the talent gap with nearly two million skilled workers before 2027.
- Green Electronics: New rules require recyclability and power efficiency. This is pushing brands to think about e-waste and green energy tech—finally.
- Focus on Innovation: Over 400 Indian tech startups were founded last year in electronics design and manufacturing. Some even bagged global patents in IoT and AI hardware.
Here’s a quick look at India’s electronics targets using the government’s most recent data:
Year | Electronics Manufacturing Value (USD Billion) |
---|---|
2023 | 155 |
2025 | 200 |
2027 (projected) | 300+ |
The next few years are all about rapid, smart moves. If you’re investing or job-hunting in electronics manufacturing in India, keep an eye on companies putting money into automation, AI-powered tools, and eco-friendly designs. Partnering with engineering institutes or jumping on government PLI incentives is also a no-brainer. There’s never been a better time to get hands-on and build something real in this industry.