Understanding the financial commitment required to establish a factory is a crucial step for any aspiring entrepreneur in the manufacturing sector. It's not just about setting aside a chunk of cash; it's about deeply understanding where those dollars will go and how to make them work for you.
From the location you choose to the equipment you invest in, each decision impacts the overall cost, requiring an informed approach. But it's more than just numbers. It's also about aligning your investments with your long-term business vision.
This article aims to guide you through the essential cost considerations in factory building, helping you anticipate the financial landscape of your manufacturing venture and make informed decisions.
- Understanding Initial Costs
- Factors Influencing Factory Costs
- Choosing the Right Location
- Equipment and Technology Investments
- Navigating Regulatory and Legal Requirements
Understanding Initial Costs
Embarking on the journey to set up a factory means grappling with a mosaic of expenses that can quickly add up if not carefully managed. It's not just the massive edifice and fancy machinery; there’s a robust spectrum of costs lurking beneath the surface that need your attention. These initial costs can be broadly categorized into land and construction, machinery and equipment, and the often-overlooked setup expenses.
Land acquisition and construction are the foundations of your factory adventure. Finding the right plot means balancing cost with logistical essentials, ensuring that your factory is situated in a place that makes sense for both input and output. Then comes the construction, where costs can fluctuate based on architectural design, material choice, and labor wages. Choosing a location with favorable industrial zoning can sometimes help reduce regulatory hurdles and even save on taxes.
Machinery and equipment expenses follow closely behind. This is often where a significant chunk of your budget will be allocated, particularly if you eed specialized or high-tech machines for your production processes. It’s worth considering both new and second-hand equipment, weighing reliability against cost. A smart approach would be to consult with industry experts or attend trade shows where you can witness the machinery in action and make informed decisions.
Then there are crucial setup costs, which include legal fees, licenses, and initial staffing. Legal compliance can be a maze, as each region might have differing rules and regulations. From environmental clearances to specific industry regulations, it’s important to get all legalities squared away early on to avoid any business disruptions later. Recruiting the right personnel is equally vital; they’ll be the heartbeat of your operations. Early hires might include project managers, factory supervisors, and financial analysts to set processes in motion effectively.
Let's not forget those sneaky unforeseen costs that can erupt unannounced. Allocating a decent fraction of your budget towards a contingency fund can save headaches down the line. Consider quote:
"A well-planned budget always has room for the unexpected," advises Tim Ferris in his article on startup economics.
Lastly, modern factories often face additional upfront investment if they plan on implementing sustainable practices from the get-go. While incorporating green technologies and energy-efficient systems may inflate initial costs, they could lead to substantial savings in the long term, not to mention the positive impact on brand reputation in an ever more eco-conscious world.
Factors Influencing Factory Costs
Setting up a factory involves a wide range of cost factors, each playing its part in shaping the overall expenditure. The first thing any entrepreneur should consider is the choice of location. A prime spot may offer logistical advantages like proximity to suppliers and customers, but it often comes with a hefty price tag. Zoning laws can also impact where you can build, potentially limiting options or adding to costs if the land requires rezoning. Then there's the cost of labor, which can vary dramatically based on the local economy, with urban centers typically demanding higher wages compared to rural areas. Add to this the cost of utilities such as electricity, water, and waste disposal, which differ by region and can fluctuate.
Beyond location, the size and complexity of the factory directly influence financial requirements. A larger facility obviously requires more material, from steel to concrete, driving up costs. Additionally, the type of manufacturing will dictate the interior layout and the nature of the machinery needed, making these decisions crucial early on. For instance, a **startup factory** for light assembly will have different spatial and technological needs compared to one involved in heavy manufacturing. Expanding on this, integrating advanced technology can be a significant expense but is often necessary to remain competitive. Automated systems, although costly upfront, can offer efficiency gains and reduce labor costs over time, which is a critical consideration for long-term planning.
Let's not forget the regulatory and compliance aspects. Navigating these can add initial costs in terms of both time and money. Factories must adhere to myriad local, state, and federal regulations, often requiring investments in safety equipment and environmental safeguards. Depending on the industry, certifications may be mandatory, each needing time, capital, and possibly consultancy fees to secure. A quote from Forbes suggests, "Staying ahead of regulatory demands is not just about compliance—it’s a way to ensure sustainability and focus on innovations." This aspect cannot be overlooked, especially in sectors like chemicals or pharmaceuticals, where regulatory environments are particularly stringent.
Finally, entrepreneurs need to gauge the cost of capital and financing options. Conventional bank loans, venture capital, or government grants each carry different financial implications. Interest rates and repayment terms can significantly impact cash flow, so it is critical to evaluate these options carefully. A detailed financial plan must account for all these expenses, ensuring adequate funding is in place from day one. Strategic planning in this area not only safeguards against unforeseen financial burdens but also positions the factory for eventual growth and scaling. As the industry adage goes, "financing often becomes the bridge between a startup idea and a thriving business."
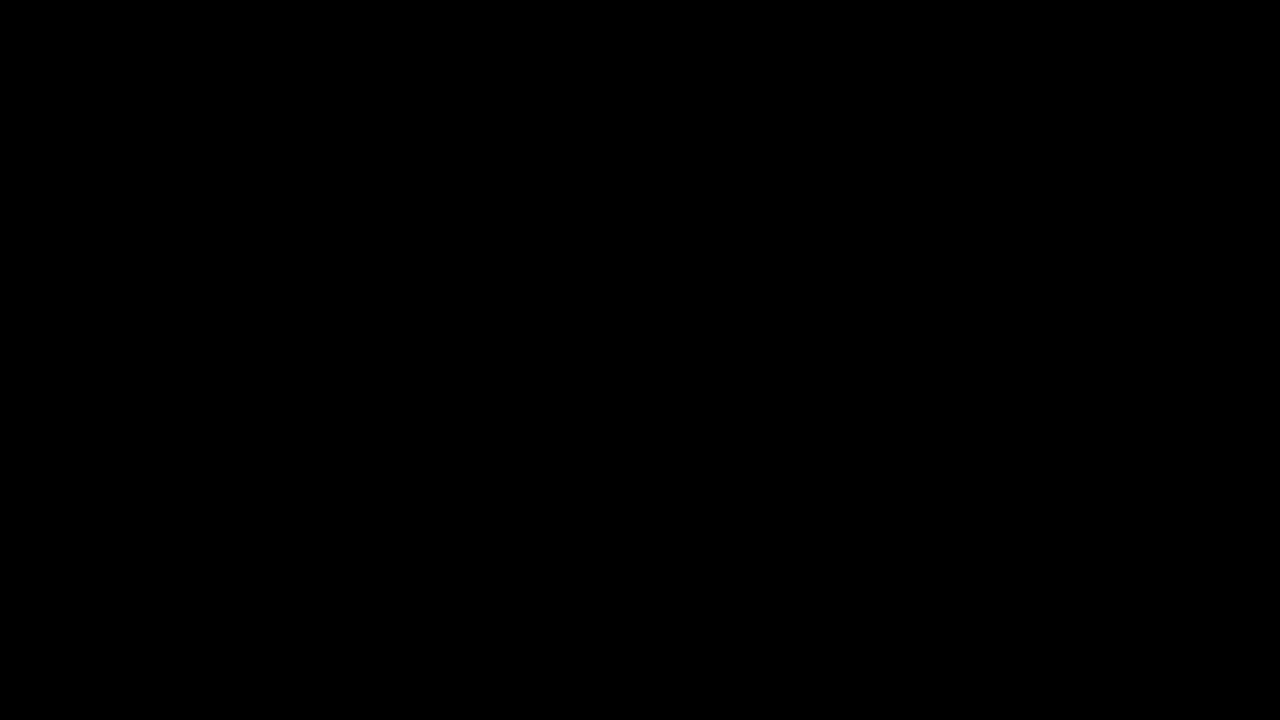
Choosing the Right Location
One of the most critical decisions in building a factory is selecting the right location. It's more than just a pin on a map; it involves a complex matrix of factors that can all significantly affect the bottom line. When finding an appropriate place, business owners should consider the accessibility to major transport routes. Proximity to highways, ports, and rail lines can dramatically reduce logistics costs, making the factory more competitive in the long run. There's also the question of labor availability, where being situated in regions with skilled labor pools can make a significant difference, not only in hiring but in maintaining production quality and consistency.
Additionally, startups should assess the cost-effectiveness of utility supplies in the area. For example, regions with abundant, cheap energy sources can provide an economic advantage, especially for industries that consume a lot of power. Striking the perfect balance between infrastructure costs and utility expenses is crucial. Tax incentives and government grants are another aspect to look into, as many regions offer attractive financial benefits to lure manufacturing investments. The local regulatory environment should not be overlooked as well, as compliance with environmental and safety regulations can vary significantly from one jurisdiction to another.
Understanding the community where you plan to build your factory is equally important. Local market potential can dictate not only the demand for your products but also the supply chain possibilities. Close ties with local suppliers and distributors can cement a strong customer base early on. Cultural considerations might also play a role. Different areas may have unique business practices and cultural nuances that can influence the operation. It’s also wise to consider the political climate of the region. Unstable political environments can pose risks to factory operations, while politically stable areas generally promise more security for investments.
According to a report from the World Bank, "The right location can not only enhance operational efficiency but can significantly contribute to the economic prosperity of the business."
Moreover, no decision about location can be complete without a thorough risk assessment. Factors like the threat of natural disasters, such as floods and earthquakes, can pose enormous threats to a manufacturing investment. Installing the requisite infrastructure and safety measures can be a costly affair, adding unforeseen expenses to your plan. Thoroughly researching historical data and consulting local geographical and meteorological experts can help mitigate these risks. The role of technology in selecting a location is worth mentioning as well. Geographic Information Systems (GIS) technology can provide detailed insights about demographic patterns, economic activity, and other essential data to help make an informed decision.
Equipment and Technology Investments
Investing in the right equipment and technology is crucial when setting up a factory. It is not just about purchasing the latest gadgets but ensuring these tools align with your production goals. The type of equipment you need will largely depend on the kind of manufacturing you're involved in. For example, a textile mill would require looms and dyeing machinery, whereas a food processing plant might need ovens, mixers, and packaging equipment. One common misconception is that newer technology always translates to better efficiency. However, the focus should be on how well the equipment integrates into existing processes and its overall impact on productivity.
Budgeting for equipment is a delicate balance. It’s essential to conduct a thorough cost-benefit analysis to understand the long-term impact of your investments. Initial costs can be high, but investing in durable, energy-efficient machinery can help save on operation costs over time. Entrepreneurs also need to consider whether to buy or lease equipment. Leasing might have lower upfront costs and allow easier upgrades, but buying can provide more control and long-term savings. A strategic approach could involve a mix of both, depending on the equipment's life span and your business model.
Keeping pace with technological advancements is another consideration. Investing in technology such as automated systems or cloud-based management tools can significantly enhance productivity and streamline operations. Automation, for example, can reduce error rates, increase output, and free up valuable human resources for more complex tasks. However, it also requires additional investment in training staff to manage and maintain these systems effectively. According to a 2022 survey by Deloitte, factories embracing advanced technologies experienced a 15% improvement in operational performance within the first year.
"The right mix of technology can transform a factory's efficiency," says Sarah White, CTO at a leading industrial consultancy. "But remember, it's not about replacing human expertise but enhancing it."
It's crucial to consider the future needs of your business when planning technology investments. Flexible and scalable solutions can be invaluable as your factory grows. Start with a clear roadmap that outlines not just the immediate equipment needs but anticipates future technology upgrades as well. This step will help in making informed decisions that won’t become obsolete in a few years. Also, remember to consider the maintenance and service contracts of the equipment as part of your initial purchase. These can significantly impact your long-term operational costs. A well-planned strategy for equipment and technology investments ensures that your factory remains efficient, cost-effective, and competitive in the global market.
Here is a quick overview of the potential benefits and considerations when investing in factory equipment and technology:
Investment Area | Benefits | Considerations |
---|---|---|
Automated Systems | Reduced errors, increased efficiency | Training costs, integration with current systems |
Energy-Efficient Machinery | Lower long-term costs, environmentally friendly | Higher initial investment |
Cloud-Based Management Tools | Improved data accessibility, better resource management | Data security, subscription fees |
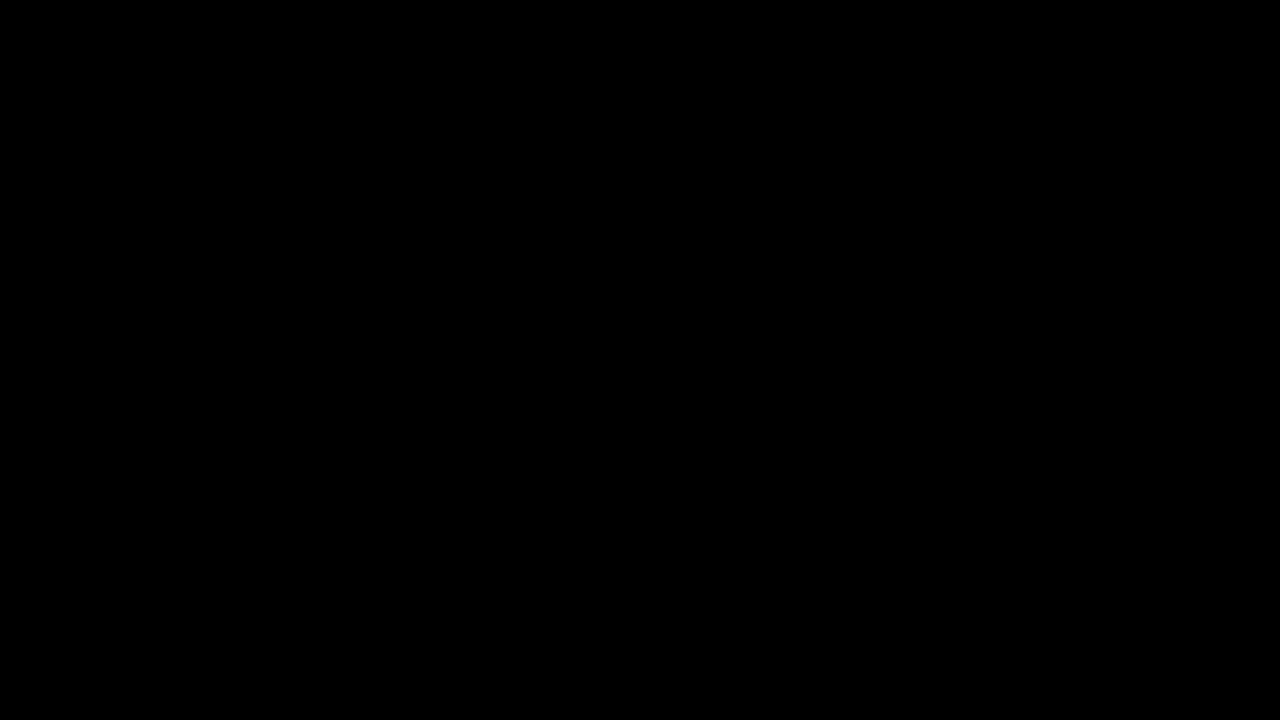
Navigating Regulatory and Legal Requirements
Entering the world of manufacturing is not just about setting up machines and hiring workers. It involves navigating a complex web of regulatory and legal requirements that can be daunting for newcomers. The costs associated with meeting these regulations can be significant, yet they are crucial to ensure the smooth operation of your factory. Understanding the laws that govern your industry is critical from the start.
Depending on the type of manufacturing you engage in, you'll need to comply with numerous local, state, and federal regulations. These regulations are designed not only to protect the environment and public health but also to maintain fair labor standards. For instance, environmental laws like air and water quality standards can affect your choice of equipment and processes, potentially leading to higher upfront costs but ensuring long-term sustainability. Familiarizing yourself with these regulations early can save you from costly fines and work stoppages in the future.
"The success of any manufacturing endeavor is as much about understanding the market as it is about mastering the regulatory landscape," says Michael Blythe, a prominent industry analyst.One important aspect is obtaining the necessary permits and licenses before commencing operations. This can vary significantly depending on your location and the scale of your operation. For example, a small-scale operation may only need a basic occupational license, while a larger facility might require multiple permits concerning emissions, waste disposal, and health and safety compliance. Neglecting these legalities can halt production and lead to financial penalties.
The importance of labor laws cannot be overstated. Ensuring fair wages, safe working conditions, and proper benefits are not only legal requirements but moral imperatives. Compliance with the Occupational Safety and Health Administration (OSHA) standards, for instance, is vital to protect both your employees and your business against liability claims. Legal compliance management calls for regular employee training, up-to-date records, and perhaps even hiring a specialist to oversee compliance issues. Preparing for unforeseen challenges is another key consideration.
If you're planning to open a startup factory abroad, the legal landscape becomes even more intricate. Every country has its own set of challenges, from varying labor laws to different environmental standards. Establishing a compliance system is essential. A proactive approach involves not only adhering to current laws but also anticipating how those regulations might evolve over time. This forward-thinking strategy ensures your manufacturing investment remains secure against legal challenges.
Finally, it may be beneficial to consult with a legal expert specializing in construction, licensing, or production setup to tailor your strategy. Legal consultants can offer insights that align your business model with regulatory requirements, providing peace of mind and allowing you to focus on other crucial aspects of business development. With the right preparation, navigating these regulatory waters becomes less about obstacles and more about opportunities for growth and innovation in manufacturing.