Steel manufacturing has been an integral part of the United States' industrial journey, building the foundations of cities and driving economic growth. But how exactly does steel production fit into the modern American industrial landscape? 2025 finds us in a world increasingly aware of environmental impact and economic sustainability, making these questions more pertinent than ever.
As international competition heats up and technological innovations flood the market, American steel-makers have had to adapt. They've shown resilience by embracing modern advancements and sustainable practices to not only survive but thrive. Journey with us as we explore the past, present, and future of steel in America, highlighting the resilience and adaptability of an industry that refuses to rust.
- The History of Steel Production in the USA
- Key Players and Locations
- Innovations and Sustainable Practices
- Challenges and Future Prospects
The History of Steel Production in the USA
When pondering the essence of American industry, one cannot neglect the significant role that steel manufacturing has played. The roots of steel production in the United States stretch back to the early 19th century, marking an era of newfound industrial aspirations. It all began with iron, the precursor to steel, which was utilized extensively during the colonial period. However, it wasn't until the discovery of iron ore in the Great Lakes region that the potential for steel production truly began to take form.
By the mid-1800s, the U.S. saw the construction of pioneering mills, with Andrew Carnegie at the forefront during the steel boom. The growth of the railroad system was instrumental in this rapid expansion, as the demand for durable materials surged. Amidst this rise, the invention of the Bessemer process in the late 1850s was a game-changer, making mass production of steel economically viable and sparking exponential growth in the industry.
The turn of the 20th century witnessed the United States becoming the leading steel producer globally. Major cities such as Pittsburgh evolved into thriving steel hubs, earning it the moniker "Steel City." This period also saw the rise of influential companies like U.S. Steel, all of which played vital roles in shaping the economic landscape. But, as the industry flourished domestically, it wasn't long before the effects of globalization started to be felt. The latter half of the 20th century brought declines in production due to international competition and shifting economic conditions.
Despite these challenges, the industry showed resilience. Companies began to incorporate technological advancements and explore more sustainable practices to maintain their competitiveness. A significant focus was placed on recycling, with more than 70% of steel today being recycled. As interestingly noted by a leading historian, "Steel mirrors the American spirit – when faced with adversity, it adapts, strengthens, and redefines itself."
The economic struggles of the late 20th and early 21st century did not dampen spirits. Recent years have seen a resurgence in American steel production, driven by advancements in electric arc furnaces and improvements in production efficiency. Companies are increasingly focusing on environmentally friendly solutions, adapting to a world where sustainability is no longer a choice, but a necessity.
An intriguing observation is that while the industry contracts and expands, it remains a steadfast component of America's industrial identity. The saga of steel production in the USA is a testament to a networked blend of tradition, innovation, and resilience, proving that even after all these years, the heart of American industry continues to pound with a metallic spirit.
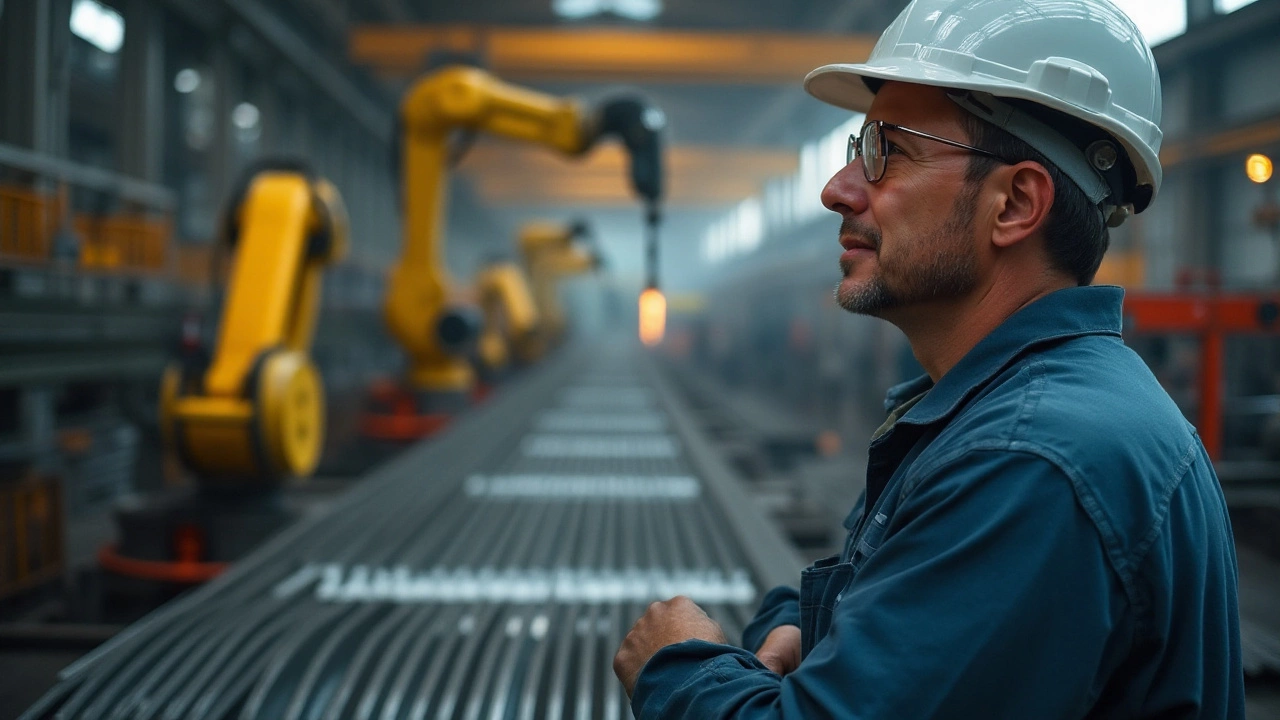
Key Players and Locations
The realm of steel manufacturing in the USA is bustling with major industry giants and lesser-known, yet impactful players. At the forefront is Nucor Corporation, an industry leader renowned for its innovative electric arc furnace technology. Forging a progressive path, Nucor maintains a network of mini-mills scattered across the country, ensuring local economies benefit from domestic steel production. Another key player, U.S. Steel Corporation, with its historic roots traced back to the early 20th century, continues to be a pivotal character in shaping the modern American infrastructure.
Speaking of locations, the Great Lakes region, often dubbed the 'Steel Belt', plays host to a concentration of significant steel plants. This region offers not only strategic access to waterways for transport but also proximity to coal and iron ore resources, critical to traditional steel-making processes. In recent years, states like Indiana and Ohio have become hubs for USA steel production, balancing the scales between progress and sustainability. Not to be overlooked, the Southern states are gaining traction; Alabama's burgeoning steel sector has seen massive investments aimed at reinforcing local growth and job creation.
In the pursuit of sustainable and smarter steel-making, companies such as ArcelorMittal USA (recently acquired by Cleveland-Cliffs Inc.) have leaned into technological advancements to modernize facilities and reduce the carbon footprint. Deep inside the manufacturing maze, robots are now integral to the procedure, ensuring precision and improving safety in what has traditionally been a labor-intensive industry.
"Our commitment is not only towards production but also towards a greener planet. We leverage technology to match this dual stride," says a reputed industrial expert from Cleveland-Cliffs.As American industry players engage in fierce competition, some have also ventured into the realm of collaborative efforts, sharing insights and strategies that spark collective growth.
Interestingly, a marked trend in the industry is the resurrection of closed plants, re-purposed and re-calibrated to adhere to modern standards and output demands. Often, these revitalized sites have transformed into high-efficiency, low-emission models of steel production. With an eye on the future, companies find a balance by training their workforce in updated skill sets, aware that adaptability equates to resilience. This attention to workforce evolution ensures that as technology progresses, human capital does too, standing as a testament to America's industrial ingenuity and resilience in steel manufacturing.
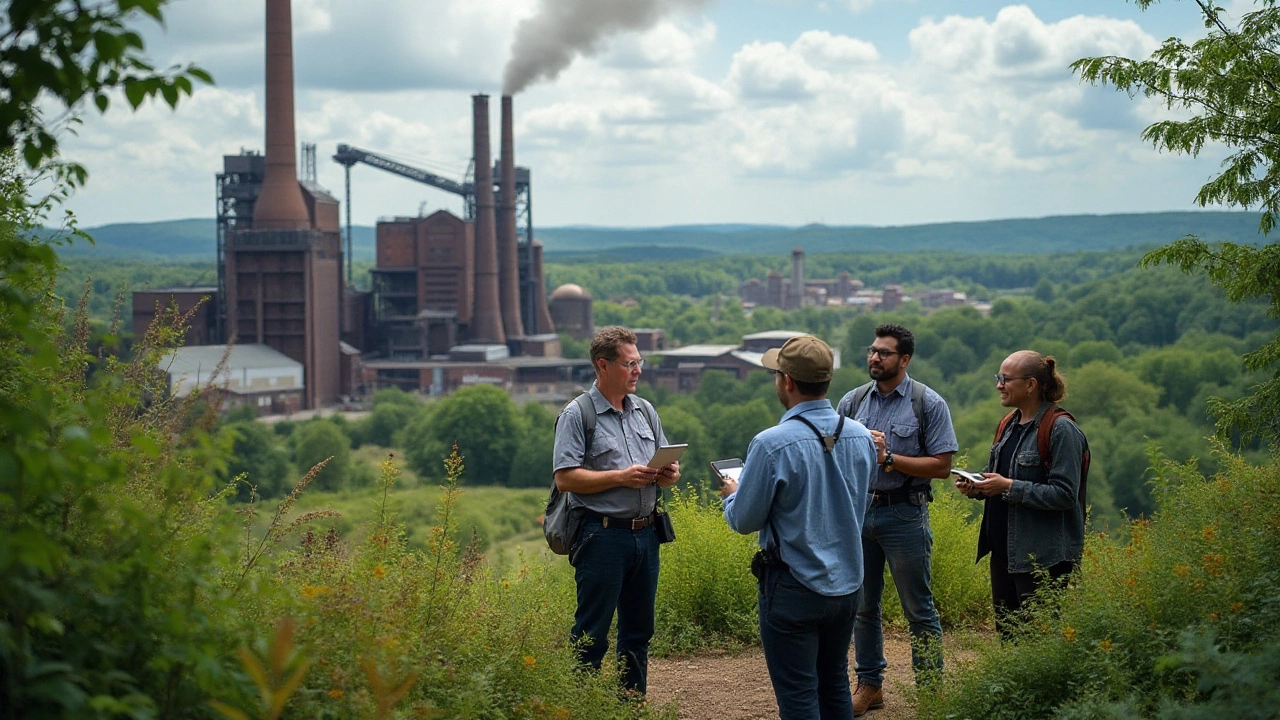
Innovations and Sustainable Practices
The American steel manufacturing landscape is experiencing a transformative phase, driven by fresh innovations and a growing commitment to sustainable practices. Cutting-edge technologies are reshaping how steel is produced, making it cleaner and more efficient than ever before. New methods, such as electric arc furnaces, have significantly reduced the environmental footprint, consuming less energy and utilizing scrap metal as raw material. This process not only conserves natural resources but also helps in managing waste effectively. Such innovations are not just technical leaps but essential steps towards a greener future.
The push for sustainability extends beyond just production methods to the very materials used. Many steel manufacturers are investing in research to develop high-strength, lightweight alloys that offer the same durability as traditional steel but require less material and energy to produce. This shift supports industries, including automotive and construction, in their quests for fuel efficiency and reduced emissions. Additionally, there's a significant move towards the integration of renewable energy sources, such as solar and wind, into steel production facilities, further diminishing reliance on fossil fuels.
One of the inspiring aspects of this evolution is the industry's collaborative efforts. Associations and universities are working together to foster innovation. For instance, the collaboration between MIT and major steel producers aims to create zero-emission and energy-positive steel plants. As Dr. Jane Hart, a leading researcher, noted,
"Innovations in steel production are not just beneficial for the environment; they're paving the way for new economic opportunities and job creation."Such partnerships underscore the sense of shared purpose driving the sector forward.
Additionally, the digital revolution is leaving its mark. Smart manufacturing techniques, utilizing Industrial AI and IoT, enhance operational efficiency and reduce waste. Real-time data analytics enables plants to optimize processes and predict maintenance needs, cutting downtime and boosting productivity. These technologies offer a glimpse into a future where steel production is not only cost-effective but also significantly kinder to the planet.
The commitment to sustainability is further backed by impressive statistics. According to a recent industry report, the energy intensity for producing steel has dropped by 25% over the past decade due to these innovations.
Year | Energy Intensity Reduction (%) |
---|---|
2015 | 18% |
2020 | 21% |
2025 | 25% |
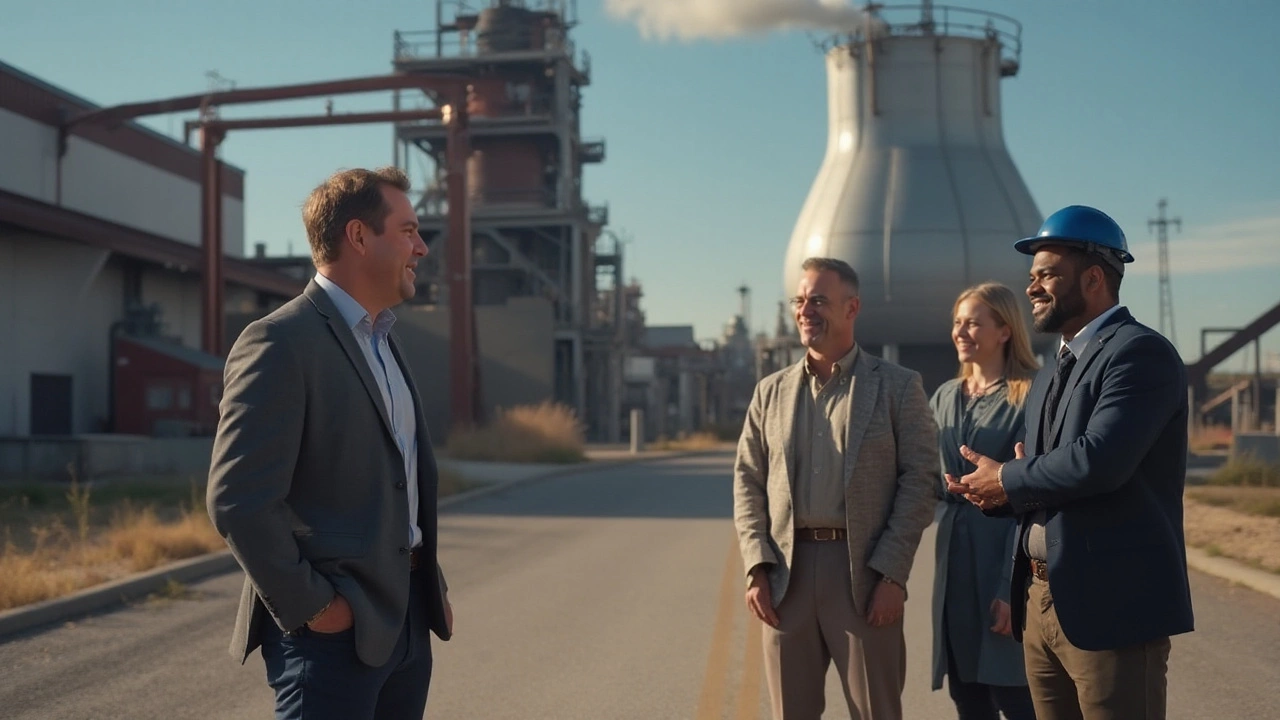
Challenges and Future Prospects
As the steel industry in the United States moves into 2025, it faces a landscape that is both challenging and full of potential. International trade tensions have long been a thorny issue for American steel manufacturing, with competition from international markets, particularly from China, pressing heavily on pricing and production capacities. Despite these pressures, U.S. steel manufacturers have been actively seeking adaptation, by re-tooling their approaches and markets. Energy consumption and the considerable carbon footprint of steel production remain crucial hurdles, driving the industry’s shift toward more sustainable practices. It's undeniable that these environmental considerations are shaping the future of steel, as regulations become stricter and public awareness grows.
Technological advancements are forging new pathways for USA steel production. Modern techniques like electric arc furnaces offer a more flexible and environmentally friendly alternative to traditional blast furnaces. Companies are investing in artificial intelligence and automation to enhance production efficiency and reduce costs, allowing them to stay competitive on the global stage. The integration of such innovations not only enhances the quality and production speed but also improves safety conditions, a significant concern historically.
"Adaptability and innovation are not just survival tactics but thrive strategies," said John Ferriola, former CEO of Nucor Corporation, highlighting the industry’s forward-thinking approach.
Despite these technological advances, unpredictability in raw material prices continues to be a concern that can impact profitability and operational planning. Political dynamics and tariff alterations pose additional risks that can disrupt steady progress. Yet, the resilience seen over the past decades, withstanding economic shifts and policy changes, assures a measure of confidence that the American steel industry will continue to stand strong. American industry cannot afford complacency, as there is a constant need for investment in research for new uses of steel and potentially exploring alternative markets, such as recycling and reusing scrap.
Moving forward, collaborative efforts between government bodies and industry leaders are crucial. Policies targeting innovation incentives and infrastructure development can play a significant role. Strengthening domestic demand through robust investment in infrastructure is anticipated to offer a steady foundation for growth in this sector. Corporate partnerships, cross-industry collaborations, and strategic alliances are likely to become more prevalent, facilitating knowledge exchange and resource optimization. The future roadmap involves a blend of addressing immediate challenges while pursuing long-term sustainable objectives, which can ultimately offer prosperity for the American steel manufacturing landscape.