Ever walked through a factory and noticed parts sitting around, machines waiting for instructions, or workers just standing by? That’s wasted money, plain and simple. The shocking thing is, research from the Lean Enterprise Institute found that less than 5% of the time in a manufacturing plant is spent actually adding value to a product. The rest is lost to things that don’t directly serve the customer. This is where the idea of the seven wastes comes in—one of the most important concepts in lean manufacturing. If you get your head around these, you start spotting money leaks all around your operation, big or small.
The Core Seven: What Are the 7 Wastes of Manufacturing?
The seven wastes are often called “Muda,” a Japanese term for any activity that uses resources but creates no value. Taiichi Ohno from Toyota first spelled these out, and they’ve become a kind of factory bible worldwide. Let’s break down the classic seven:
- Overproduction: Making more than you need or making it too soon. Imagine a bakery making 1,000 loaves when there’s demand for only 500. That extra bread might go stale before anyone eats it. In factories, it’s the same story—too many parts or products jam up storage and eat cash.
- Waiting: Equipment, materials, or workers sitting idle. Sometimes it’s a machine waiting on maintenance, sometimes workers waiting for instructions or materials. For some plants, up to 40% of production time is pure waiting.
- Transport: Unnecessary movement of goods or materials. If parts zigzag across half a mile of factory just to get a hole drilled, that’s a waste. Transport adds costs, increases risk of damage, and doesn’t make the product better.
- Overprocessing: Using more complex or expensive processes than needed. Why polish a hidden screw until it shines? Or use a $50,000 laser when a $500 drill press will do the job?
- Inventory: Keeping more raw materials, components, or finished goods than needed. Inventory ties up cash, crowds the plant, ages on the shelves, and can mask problems in production.
- Motion: Extra movement by people. It’s workers reaching, walking, or twisting too much because tools, parts, or controls aren’t laid out logically. Not only is this inefficient, but it leads to fatigue and injuries. A recent health study in India found that 30% of manufacturing injuries link directly to unnecessary motion.
- Defects: Products or parts that need rework or get scrapped. Each defect means wasted labor, materials, and time. Even small defect rates add up fast—think: 1% of 100,000 units is 1,000 items lost!
Each waste eats into profits but can be tackled if you know what you’re looking for. Here’s a quick data snapshot from a real-world electronics manufacturer:
Type of Waste | Estimated Cost per Year |
---|---|
Overproduction | $600,000 |
Waiting | $400,000 |
Transport | $250,000 |
Overprocessing | $120,000 |
Inventory | $800,000 |
Motion | $50,000 |
Defects | $300,000 |
Ouch, right? These aren't small numbers. Each category bleeds cash—even the so-called little ones.
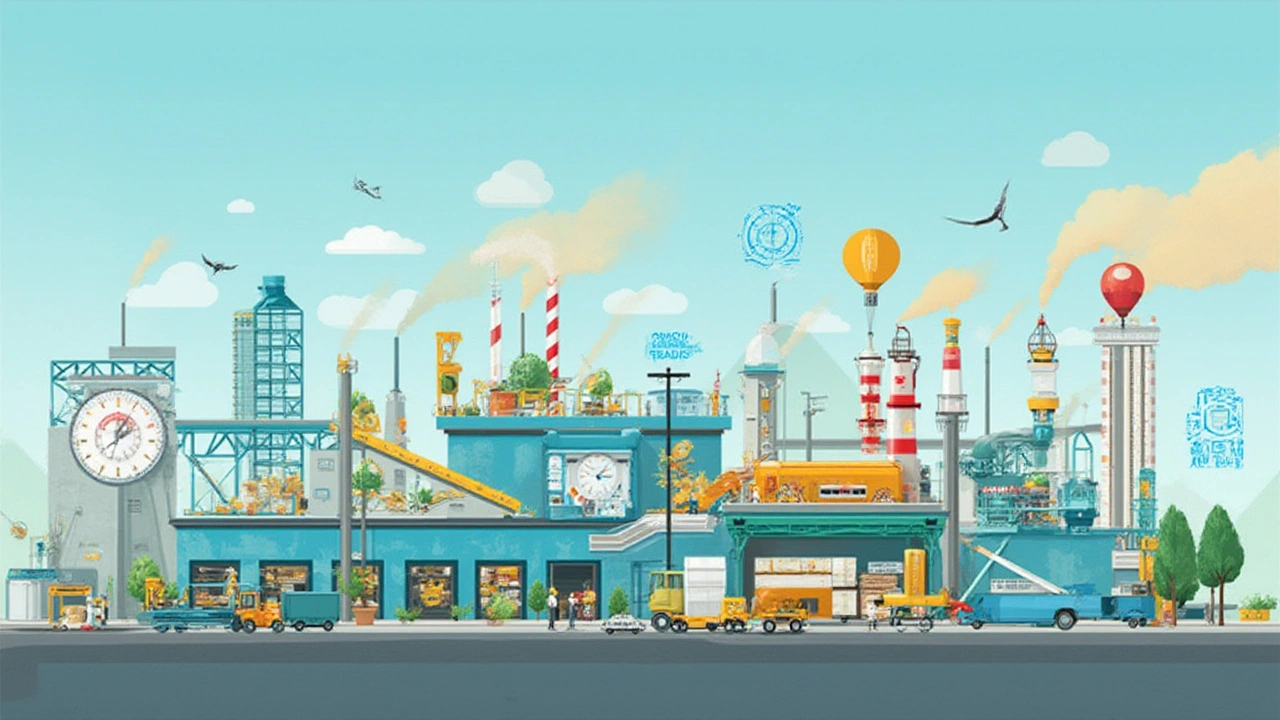
Why Do These Wastes Happen and How Do You Spot Them?
It’s not always laziness or incompetence—most workers and managers want things to run well. Wastes creep in over time because of new equipment, rushed orders, complicated processes, or simply “the way we’ve always done it.” Overproduction often comes from trying to 'work ahead' fearing shortages or downtime. Waiting is often a sign of process mismatch—maybe the paint shop gets jammed until parts arrive from welding. Excess motion? Often it comes from bad layout. A funny story: a friend of mine, Rahul, worked in a factory where the main tool chest was a football field away from the assembly line. Fixing it was as simple as rolling the chest next to the workstations, saving people hours of walking a week.
Lean manufacturing tools, like value stream mapping, 5S, and root cause analysis, are great for going Sherlock Holmes on these problems. Value stream mapping helps you trace every step in your process, showing you exactly where waste stacks up. 5S (Sort, Set in order, Shine, Standardize, Sustain) keeps workspaces tidy and logical. Doesn’t sound glamorous until you realize a cleaner bench often means 20% fewer motion wastes. Even something as small as color-coded bins can transform a messy workstation and save minutes—or hours—each day.
- Bottlenecks: If one step is always slower, backup builds up there. Watch for spots with inventory pile-up or lines of workers waiting.
- Rework areas: If there’s a space dedicated just to fixing defects, something is broken upstream—fix it, don’t just treat the symptoms.
- Warehouse tours: Take a walk, and look for parts or products gathering dust or packed in weird spots. Why are they there?
- Employee feedback: The folks on the floor usually know where the biggest frustrations are. Ask what tools they wish they had, or what steps feel pointless.
Spotting waste takes sharp eyes and honest questions. To make things real, document with photos, walk the process, and talk to the team. You can even try a technique called "the 5 Whys": for each waste, ask "why?" five times to get to the root cause. If your team’s waiting hours for material, don’t just speed up delivery—look at why the material wasn’t ready when needed.
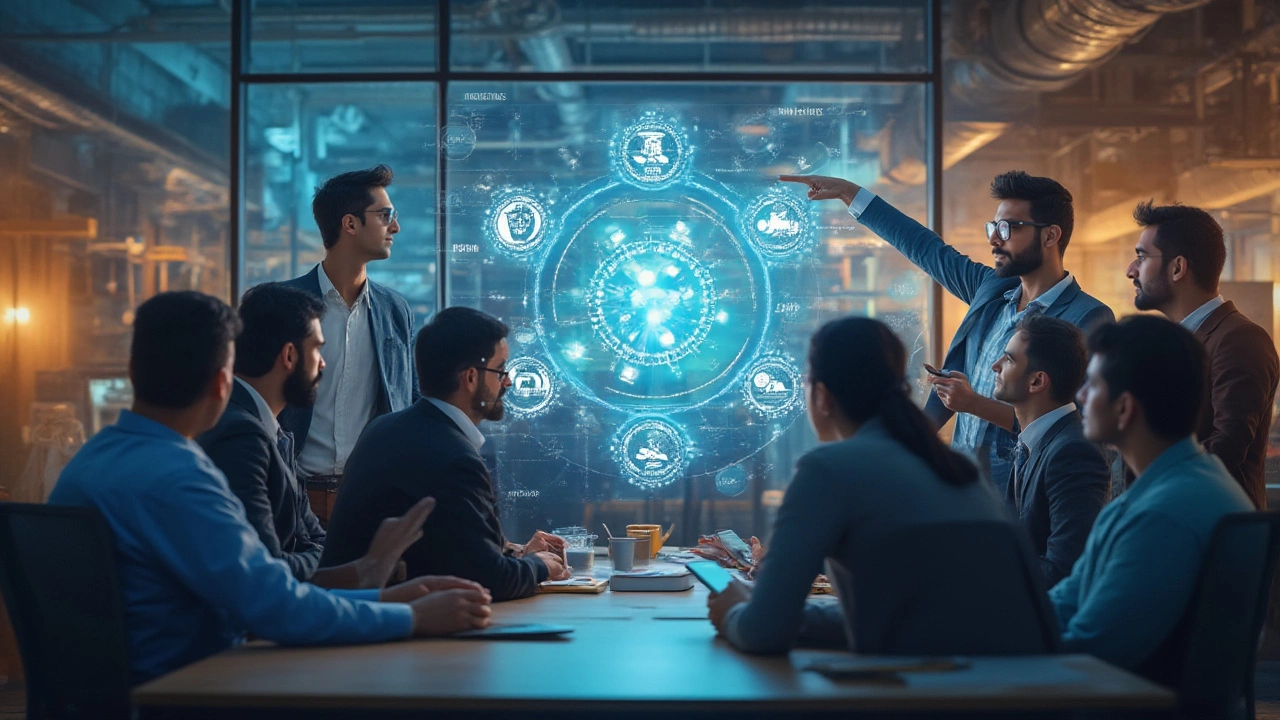
How to Reduce Wastes: Real-World Fixes from the Factory Floor
Once you’ve got your eyes open, the big question is what to do next. Here’s something wild: McKinsey reported that companies practicing lean can see productivity jumps between 15% and 50%. That’s not some niche theory—it’s happening in car plants in Chennai, plastic molders in Vietnam, even mom-and-pop hardware makers in Gujarat.
- Pull, not push: Switch to producing only what’s needed, when it’s needed. This “pull” system is the heart of lean. It stops overproduction and trims inventory. Some factories use kanban cards or electronic systems: workers only move or make more parts when there’s a real demand, not “just in case.”
- Standard work: Making every job repeatable and reliable helps clear confusion and prevent overprocessing or defects.
- SMED and setup reduction: Quick-change setups between products means you don’t need long production runs and big inventories to make changeover 'worthwhile.'
- Layout tweaks: Move tools, benches, and materials closer to where the action happens—like Rahul’s factory and their rolling toolbox.
- Visual management: Paint floor lines, use light signals, or hang boards showing real-time progress. The best shop floors tell you what’s happening at a glance. Even simple tricks like shadow boards (outlines for where each tool belongs) help cut motion waste.
- Kaizen: A Japanese word for constant improvement. The idea is everyone, not just bosses, is looking for ways to make things better each day.
Real talk—Aisha, my wife, runs a small jewelry workshop. She did a Friday “waste hunt” with her team, listing each time they waited, moved too much, or found extra parts lying around. They cut a few steps, shuffled tables, and started labeling parts bins. Even in a tiny shop, they saw a 20% faster order turnaround in just two weeks.
Of course, not every fix is easy. You’ll bump into old habits and resistance. But keeping employees involved, asking for their ideas, and showing quick wins helps break through. Little by little, those small changes stack up to big savings—sometimes worth crores in the long run.
The bottom line? Manufacturing waste isn’t invisible magic—it’s real, and you can fix it. With a sharp eye, the right tools, and a willingness to ask “why,” anyone can start plugging those leaks. Don’t just walk past a pile of dusty parts or a motion-heavy workstation. Dig deeper, and you’ll start seeing opportunities nobody else does. That’s how the best manufacturers pull ahead—and keep winning year after year.