In a world where steel is woven into the fabric of contemporary life—supporting skylines, forming vehicles, and shaping countless aspects from bridges to skyscrapers—a pressing question buffs through the industrial haze: Who truly rules the steel industry?
Understanding the kingpins of the steel sector requires a journey into the histories and latest paradigms of global steelmakers. It involves exploring the enormity of production figures balanced with a commitment to innovation and sustainability—factors that define modern champions of this industry.
This article ventures into the complex dimensions of steel production, throwing light on the titans whose strategies and initiatives not only generate massive steel outputs but also influence global markets. Join us as we untangle the intricate web of the steel industry’s leading figures and their ever-evolving empires.
- The Evolution of Steel Giants
- Pioneers and Their Processes
- Global Impact and Innovations
- Challenges in the Modern Steel Market
- The Future of Steel Leadership
The Evolution of Steel Giants
The history of the steel industry is a testament to human ingenuity and resilience. It traces back to ancient times when blacksmiths first discovered how the combination of iron with carbon could produce an alloy far superior in strength and versatility. As civilizations grew, so did the demand and complexity of ironmaking techniques, setting the stage for a global industry that would catapult entire economies. The 19th century witnessed a dramatic transformation with the advent of the Industrial Revolution. The introduction of the Bessemer process in 1856, which enabled the mass production of steel, marked a pivotal moment in the industry. Britain's steel output rose meteorically, sparking an industrial boom that reverberated across continents. This era laid the foundation for the world’s mega steel corporations that would ignitively define the landscape of modern manufacturing.
Transition to the 20th century, and the global focus began shifting. The United States swiftly rose as a steel powerhouse with corporations like Carnegie Steel Company leading the charge. Andrew Carnegie’s empire, which flaunted steel mills spanning Pennsylvania and Midwest America, became an unprecedented industrial juggernaut. An infamous quote from Carnegie captures the spirit of this era:
"The man who acquires the ability to take full possession of his own mind may take possession of anything else to which he is justly entitled."Alongside them, Japanese steel giants entered the fray, propelled by post-war recoveries and technological advancements. As the industrial demands of the world expanded, steel production too witnessed exponential growth, punctuated by fierce competition amongst nations eyeing dominance in this vital sector.
The globalization of the global steel market brought about new and formidable players. The rise of China in the 21st century was nothing short of spectacular. Companies like Baowu Steel Group and China Baowu Steel Group Corporation emerged from this economic giant, swiftly ascending to the zenith of the steel industry hierarchy. According to the World Steel Association, China's share of global steel production soared to over half the world's output in 2022, revolutionizing the international market with its affordable prices and robust output. In this competitive atmosphere, positioning within the steel industry is secured not only by capacity but also by leveraging innovation, sustainability, and strategic mergers. This continual evolution reflects the ongoing race for supremacy in which only the most adaptive survive and thrive.
Now, the giants of the steel world navigate a multifaceted narrative—one that involves balancing economic pursuits with environmental responsibility. As climate change concerns dominate headlines, the industry is under relentless scrutiny. Efforts to pivot towards low-carbon emitting production methods have sparked an era of green steel evolution. Companies are investing heavily in recycling, minimizing waste, and adopting eco-friendly technologies. This pursuit for sustainable innovations heralds a new dawn for the steel giants, suggesting that their ability to evolve with these pressing challenges will dictate their standing in the future of the industry.
Pioneers and Their Processes
The story of the steel industry is a saga of innovation, tenacity, and engineering brilliance, helmed by pioneers whose breakthroughs have reverberated across centuries. It all started with iconic figures such as Sir Henry Bessemer, a name synonymous with pioneering steel production processes. His invention, the Bessemer Process, transformed the industry in the mid-19th century by dramatically reducing the cost and labor required to produce steel. This breakthrough catalyzed a new era of industrialization, making steel an affordable commodity that shaped our modern world. Bessemer's method focused on blowing air through molten iron, igniting carbon impurities, and producing steel in vast quantities. This process not only increased efficiency but also led to the construction booms across continents, with skyscrapers rising and railways stretching beyond horizons, fundamentally altering landscapes and economies.
The Rise of Carnegie Steel
Fast forward to the United States in the late 19th century, where Andrew Carnegie and his Carnegie Steel Company ushered in what could be considered the golden age of steel manufacturing. Carnegie adopted and improved the Bessemer process, integrating it into a remarkably efficient production system nestled along the burgeoning city of Pittsburgh. His relentless pursuit of cost-cutting innovations, coupled with vertical integration, allowed his mills to dominate the market. Carnegie's astute business practices, matched with his passion for philanthropy, left an indelible mark on both commerce and society. His words resonate through time:
“The man who dies thus rich dies disgraced.”His company's practices laid the groundwork for mass production and set standards that steelmakers adhere to today, illustrating the transformative power of strategic industry leadership.
Modern Innovators and Sustainable Practices
In the contemporary scene, giants such as ArcelorMittal and China’s Baowu Steel Group continue to lead with advanced techniques and unwavering commitment to sustainability. ArcelorMittal, recognized as one of the largest producers globally, has embraced electric arc furnace technologies to mitigate environmental impact, steering the industry towards sustainability. Their efforts in research and development have seen innovative practices in recycling and reduction of CO2 emissions, shaping the dialogue on eco-friendly production. Meanwhile, Baowu continues its ascendancy by adopting refined blast furnace techniques married with cutting-edge informatics to maintain quality and affordability. The competitive edge in today’s steel manufacturing now hinges on the efficiency of processes and the ability to innovate sustainably. With the industry at a crossroads of innovation and environmental responsibility, these pioneers lay down blueprints for future development.
Company | Annual Steel Production (Million Metric Tons) | Innovation Focus |
---|---|---|
ArcelorMittal | 89.8 | Electric Arc Furnace |
Baowu Steel | 96.3 | Blast Furnace Optimization |
The relentless drive of these steel manufacturing pioneers not only carved niches within the vast expanse of the global steel market but also mapped a future that blends industry influence with adaptable, sustainable practices. As they continue to evolve, these leaders commit not just to output, but to refining processes that align with the needs of a rapidly changing world.
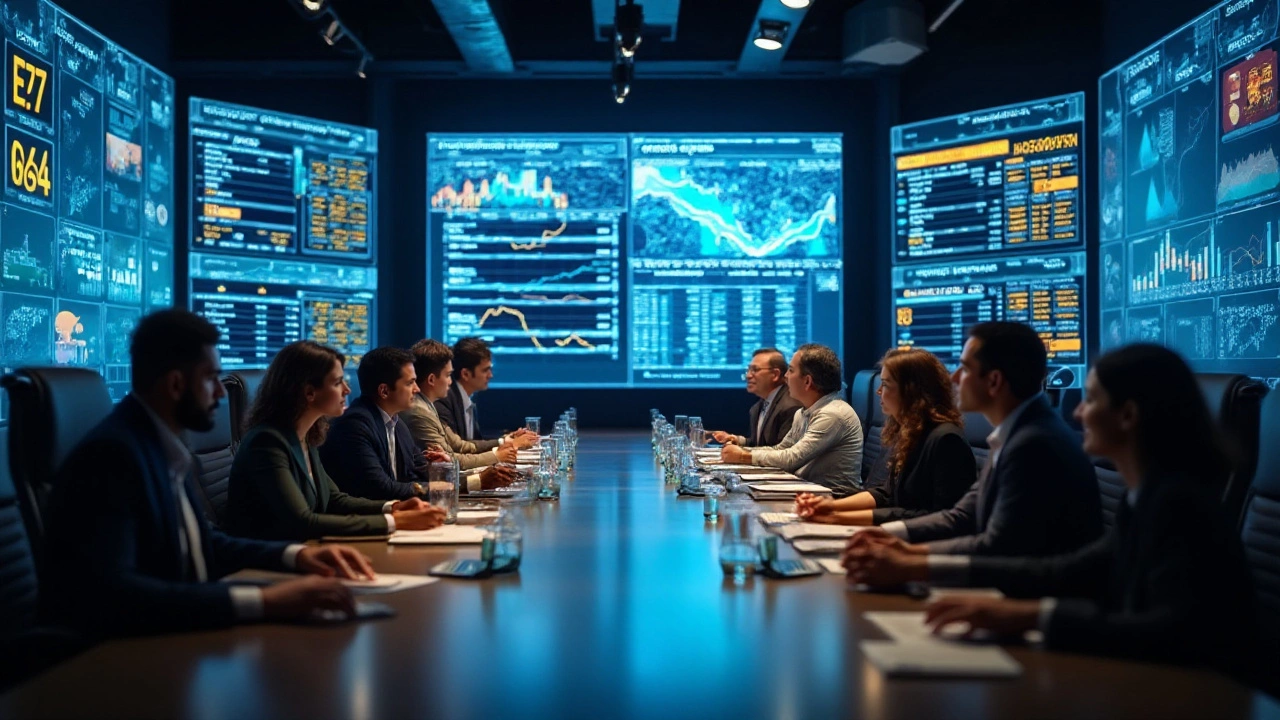
Global Impact and Innovations
The steel industry is more than just a cornerstone of infrastructure; it is a force that drives global economic dynamics. Steel, a product of both ancient craft and modern technology, influences industries as varied as automotive manufacturing to construction, reflecting the broader trends toward innovation and sustainability. In recent years, the global demand for steel has surged, driven by infrastructure developments in emerging markets and technological advancements in established ones. Some of the world's largest steel producers, such as China and India, have seen exponential growth, with China producing more than half of the worldwide steel. This dominance reshapes international trade and affects economic policies worldwide, presenting profound implications for both developing and developed nations.
In terms of innovations, today's steel manufacturers are not content with sheer quantity; they are spearheading transformations that make steel manufacturing more efficient and environmentally friendly. Advancements such as Electric Arc Furnaces (EAF), which recycle scrap steel, significantly reduce carbon footprints. Innovations extend beyond production methods to include new forms of steel, like high-strength, lightweight varieties that revolutionize industries from automotive to aerospace. This aligns with a global push toward sustainability, lowering emissions, and creating eco-friendly alternatives.
The role of digitalization cannot be overlooked when discussing the steel sector’s global impact. Technologies like Artificial Intelligence (AI) and the Internet of Things (IoT) are now integral to predictive maintenance and quality control, enhancing precision while reducing waste. According to a report by the World Steel Association, digital solutions contribute substantially to minimizing energy consumption, projecting potential savings of around 20% over the next decade. This shift towards smart manufacturing is not merely a trend; it's a strategic response to maintain competitive edge in a rapidly evolving market.
"The greatest innovation comes from embracing change, and in the steel industry, this means integrating sustainability into every stage of the process," remarked Dr. John Ferris, a leading researcher in materials engineering. This sentiment echoes the industry-wide effort to meet stringent global environmental regulations without compromising on production efficiency or quality.
Innovative giants, like ArcelorMittal, have launched initiatives targeting net-zero emissions by 2050, setting benchmarks for the rest of the industry. Their approach includes deploying carbon capture and utilization (CCU) technologies, along with exploring hydrogen as an alternate energy source in steel production. Such measures not only reduce environmental impact but also promise to redefine energy consumption within the sector.
The global steel market is a testament to how industries can impact both the environment and the economy. Innovations in this sphere are driven as much by necessity as by vision. They challenge traditional manufacturing processes and open avenues for research and development. Looking at the international playing field, the countries that actively invest in the latest technological methodologies are poised not only to optimize their steel output but also to navigate the complex economic landscapes dictated by environmental and technological imperatives.
Challenges in the Modern Steel Market
The modern steel industry faces a myriad of formidable challenges as it navigates the global stage. Amidst growing scrutiny and evolving expectations, steel manufacturing giants are pressed to address environmental impacts, market volatility, and technological advancement. One of the most talked-about issues is the carbon footprint associated with steel production. As the world turns toward greener practices, steel companies are tasked with reducing emissions. Integrating sustainable practices while maintaining profitability proves to be a delicate balance.
Equally challenging is the turbulence in global markets. Economic fluctuations can impact the demand for steel quite unpredictably. Trade tensions and tariffs add another layer of complexity. Companies often find themselves at the mercy of geopolitical forces beyond their control. An assertive strategy once lauded may become obsolete with a sudden policy shift. Maintaining agility in such an environment is crucial, yet not always possible for larger outfits bogged down by procedural inertia.
Technological disruption is another cornerstone of the industry's current landscape. Advances in material science and manufacturing processes pose both an opportunity and a threat. Those who embrace modernization can drive efficiency and innovation. However, the initial investment required can be substantial, and there lies a risk of obsolescence for those who lag behind. Companies that fail to integrate state-of-the-art technologies may see their margins squeezed tighter by the competition.
Global steel market leaders are also tasked with managing labor dynamics. As automation increases, ensuring that the workforce remains relevant and skilled imposes another significant challenge. The shift necessitates not just technological upgrades but a retraining and upskilling of personnel. Countries with large sectors reliant on traditional steel manufacturing face social and political pressures to ensure employment stability.
An additional layer of pressure comes from the rapid pace of urbanization in developing countries. The demand for steel in infrastructure development means an increased focus on cost-effective production. Simultaneously, the pressure mounts to deliver products that meet higher environmental and safety standards. Evolving regulatory landscapes greatly influence how companies must operate within different jurisdictions.
Another key observation from industry experts is the growing necessity for strategic partnerships. Companies are starting to realize that collaboration across sectors and with governments can provide a competitive edge.
"In this interconnected world, no steel manufacturer can afford to act in isolation," notes Dr. Carlos Rivera, a leading consultant in industrial technologies. "Building alliances is no longer a choice, but a necessity."This partnership-based approach allows leveraging additional resources, knowledge sharing, and risk distribution.
These challenges, though daunting, also chart a path toward transformation within the industry. While the complexities of sustainability, automation, and global politics persist, they signal a time ripe with opportunity. Those poised to innovate and adapt will likely continue shaping the steel industry landscape for years to come.
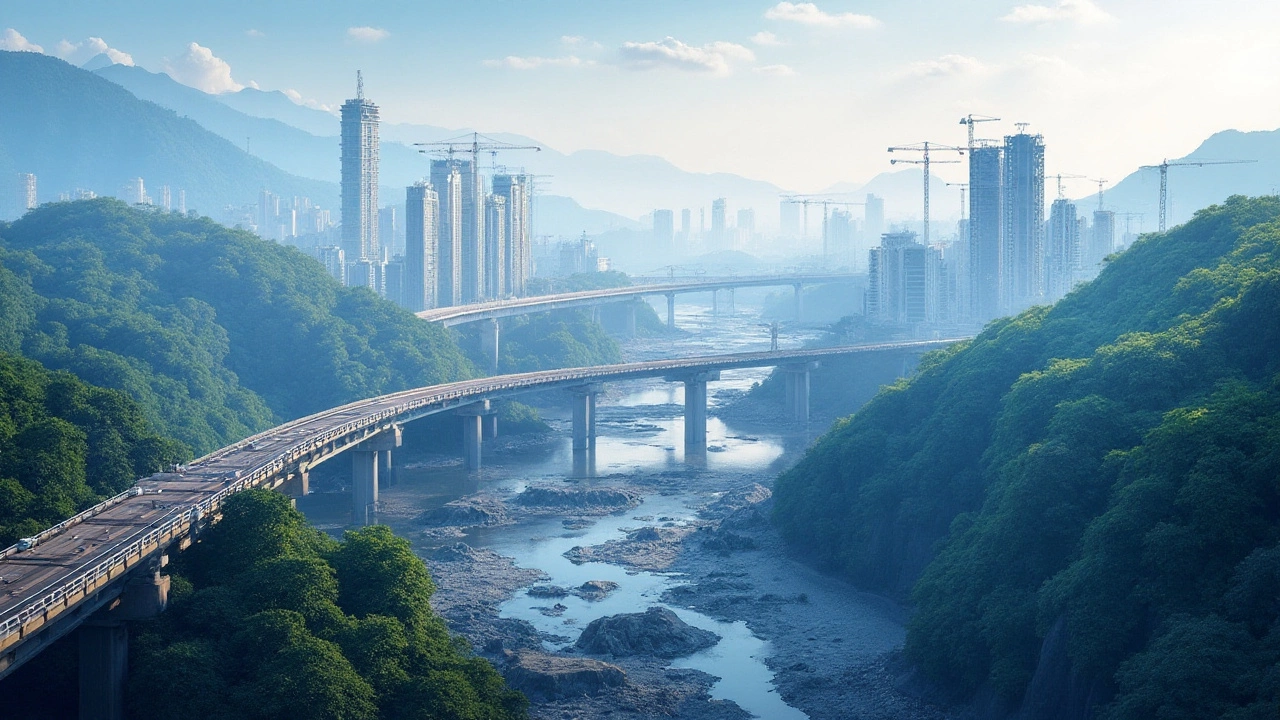
The Future of Steel Leadership
The landscape of the steel industry is on the cusp of transformative changes, as societal pressures and technological advancements drive new paradigms of leadership. Steelmakers are increasingly aware that future success is not solely anchored in quantity of output, but in the capacity to innovate sustainably and efficiently. This shift is seen through a new wave of investments in green technology, aimed at reducing carbon footprints and increasing energy efficiency. Leaders in the steel sector are drawing on renewable energy sources, with solar and wind power gradually becoming integral parts of the production process. These methods not only curb emissions but also significantly cut costs, offering a dual benefit.
Advancements in technology are reshaping steelmaking, with automation and artificial intelligence taking center stage. These innovations are being avidly adopted by the industry's frontrunners, aiming for enhanced precision and reduced waste. AI systems are now capable of predicting breakdowns before they occur, optimizing operations and thus, saving time and resources. Such technology could very well forge the path for future steel magnates, setting new standards of operational excellence and environmental responsibility.
Changing consumer demands compel steelmakers to pivot towards more specialized and high-strength steel products. This demand is fueled by industries such as automotive and construction, which seek lighter and more durable materials. Steel leaders anticipate that investing in high-grade product lines will not only meet these needs but also secure long-term contracts. Key players are therefore channeling resources into research and development, striving to lead the pack in innovations that serve the dynamic requirements of their clients.
One cannot overlook the geopolitical climate's impact on the future of global steel market leadership. Trade policies, tariffs, and international relationships continuously inhibit or boost the growth of steel production and distribution frameworks. With governments worldwide intensifying their focus on infrastructure projects, the steel demand is poised for a rebound. However, navigating the complex web of international trade will require adept leadership, adaptation, and strategically charting long-term alliances.
"Innovation, transformation, and sustainability will define the next era of the steel industry," declares Lakshmi Mittal, executive chairman of ArcelorMittal, highlighting how these elements form the bedrock of future leaders’ strategies in this sector.
By acknowledging these multifaceted challenges and opportunities, upcoming steel magnates have the chance to redefine their roles. They will not only carve their niches in the industry but also drive paradigmatic shifts toward sustainable practices, leveraging advanced technologies for a greener future. As we edge closer to this new chapter, the emerging leaders in the steel manufacturing sector will likely be those who embrace change with strategic vision, and a commitment to blending profitability with environmental stewardship.